I’d like to start off by clarifying the difference between eBoM vs eBoM. Most companies developing products have both an eBoM and mBoM.
- Engineering Bill of Materials (eBoM) — as designed
- Manufacturing Bill of Materials (mBoM) — as shipped
You may not agree, many don’t see it this clearly. The industry does, and therefore, some software tools have more ability than you may know. But, I guarantee, if you overlay these two elements onto what you are doing for Bill of Materials (BoMs), whether in Engineering, or in Manufacturing, or in Production, you’ll see the clarity of these two simple elements rise to the surface.
Definition of eBoM and mBoM:
eBoMs are created in engineering, are typically driven from the CAD tool, and are usually centric to the final assemblies list of parts or components that make up the as designed or eBoM.
mBoMs will contain, or be ‘driven’ by the eBoM. MBoMs make up the ‘end item’, or product as shipped. Of course, the eBoM, or ‘parts list’…the eBoM requires additional things like shipping containers, crates, peanuts, or packing foam, plastic bags for accessories, power cords, or items necessary to complete the product that is not defined on the eBoM.
Manual processes for eBoMs & mBoMs
In the drawing board days, we often communicated this detail as a table on the final assembly drawing. Sometimes as many sheets attached or referred to on the final assembly drawing. Hopefully, you’ve evolved beyond that! If not, that’s okay, there is hope. Unfortunately, many still use this legacy approach and are still creating (painfully) this table on their CAD assembly drawings. Others may be manually forming them in spreadsheet software.
The next step, and pain point, you must re-enter or get the data into your ERP/MRP tool. Either manually, or via an importation, it is error-prone. What if changes occur? But, that never happens, right?? Ha.
How much time does your organization spend on these tasks? How about errors because of changes? Do you have the role of Configuration Manager defined?
The task of creating the mBoM from the eBoM usually has many manual and painful disjointed steps. Often involving exporting out of one tool, into another, but only if you are evolved enough — as I stated earlier, many are not this evolved, but have the vision to do so…maybe you’ve already made a connection from your data management tool to your ERP/MRP system?
PLM Systems like PTC Windchill help you manage your BoMs
EAC can help you form this vision, and guide you to a better way of understanding this topic in the context of your organization. We strongly believe there is a better way to develop products – and managing eBoMs and mBoMs is just one part of doing it better.
PTC Windchill can drive the eBoM into the mBoM or vice versa. It has the out of the box ability to be the tool for the Configuration Manager roles in your organization. Options and variants are another use case you’ll see in a future blog topic.
Organizations have found ways to leverage PLM systems that transform their product development process and defeat pain points like the disjointed processes that come with manual creation of the mBoM from the eBoM.
Take a look at the Aberdeen PLM Research revealing that organizations with connected PLM see a 22% increase in engineering productivity and 21% improvement.
If you’re looking for a PLM solution such as PTC Windchill, our Product Development System Services (PDSS) team can help implement the software within your organization.
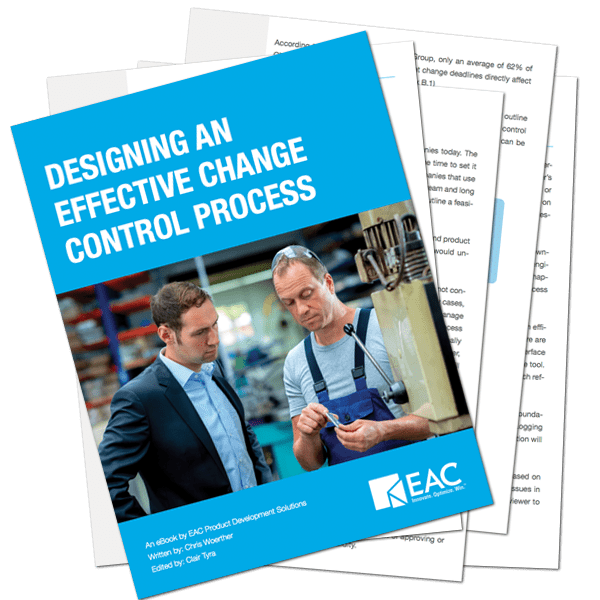
Download our free eBook on Designing an Effective Change Control Process to help understand the digital transformation movement better.