- Creo Parametric
- Design Exploration Extension
- Flexible Modeling Extension
- Human Factors
- Human Factors Analysis
- Advanced Framework Extension
- Collaboration Extension for Autodesk Inventor and SolidWorks
- Intelligent Fastener Extension
- Legacy Data Migration Extension
- Piping and Cabling Extension
- Render Studio Extension
- Mathcad Express
- Simulation Elite (Linear Structural Analysis)
PTC is changing the way Creo Design software is being sold. As of January 1st, 2018 new 3D modeling software licenses for PTC’s core solutions are only available by subscription in North America.
This makes it easier for users to utilize new functionality and keep up with the latest release of PTC Creo Parametric CAD software. It also gives organizations the flexibility to choose a 3D CAD package according to specific needs at a given time, and ensures access to the latest capabilities and premium support.
Changes in PTC Creo CAD Packaging
PTC has retired and consolidated the following CAD packages into one of 4 new tiered PTC Creo Parametric Design packages: Essentials, Essentials Plus, Essentials Premium, Engineer 1, Essentials Team, Engineer 2, Engineer 3, and Engineer 4.
You can see from the table below that Creo Design Essentials (T1) replaces Essentials, Essentials Plus, Essentials Premium, and Engineer 1; Creo Design Advanced (T2) replaces Essentials Team and Engineer 2; Creo Design Advanced Plus (T3) replaces Engineer 3; Creo Design Premium (T4) replaces Engineer 4; and Creo Design Premium Plus (T5) is an entirely new package that becomes the fifth tier for the new Creo packaging.

New PTC Creo Design Packages
With Creo Parametric and its extensions you can create, analyze, view, and share designs using 2D CAD, 3D CAD, parametric design and direct modeling capabilities along with additive manufacturing, model-based definition (MBD), and smart connected design. Every package includes the industry’s most comprehensive set of 3D CAD tools to allows you to design with maximum potential.
Every package comes with the Core Capabilities and the power to publish, share, and create augmented reality experiences right inside of your 3D CAD models. This allows you to add value to your customer experience because they can now visualize your design with AR.
Here’s a breakdown of what is included in each package:
Creo Design Essentials
Creo Design Advanced
**includes everything in Design Essentials and also includes:
- Prismatics and Multi-Surfaces Milling Extension
- Advanced Assembly Extension
Creo Design Advanced Plus
**includes everything in Design Advanced and also includes:
- Interactive Surface Design Extension II
- Behavioral Modeling Extension
- Mechanism Dynamics Extension
- Additive Manufacturing Extension – Standard
- Tolerance Analysis Extension
- GD&T Advisor Extension
- Tool Design Extension
- Expert Moldbase Extension
- Mold Machining Extension
- Layout Extension
**includes everything from Advanced Plus and also includes:
- Collaboration Extension for CATIA V4 and V5
- Collaboration Extension for NX
- Simulation Extension
- Fatigue Advisor Extension
- Flow Analysis
- GD&T Advisor Plus
- Production Machining Extension
- NC Sheetmetal Extension
- Mathcad
Creo Design Premium Plus
**includes everything from Design Premium and also includes:
- Advanced Simulation Extension
- Complete Machining Extension
- Flow Analysis Plus
- Options Modeler Extension
- Topology Optimization
- Additive Manufacturing Extension – Plus
For more details on the extensions in each of the new packages, watch our webinar replay, “New PTC Creo Design Packages Overview.”
FAQ on New Packaging
Q: What is the price for existing customers upgrading to the new packages?
A: If you already have a subscription license, then you may upgrade to the new packaging through a contract amendment. If you are still on a perpetual license, then you may convert and upgrade at the same time and pay the subscription conversion price.
Q: Do the new packages contain PTC Windchill?
A: Creo Design Advanced (Tier 2) contains Windchill PDM essentials. Design Advanced Plus, Design Premium, and Design Premium Plus is bundled with Navigate Author, MCAD Data Management I, BOM Management, and Project Management at no increased cost. These three packages will also be available without PDM.
- Q: Do we offer node-locked licenses?
A: We offer a locked license for Design Essentials and Design Advanced only.
Q: Can I still buy Creo extensions that are now bundled in the new packages?
A: Yes, all extensions will still be available to be purchased separately. If you are subscribing to a new package that does not contain an extension that you need, that extension will be available separately.
Q: Are trials for the Creo software available online?
A: Yes, you can download a free 30-day trial here
Q: How would upgrades work if I already have subscription license? Do I pay the difference on the remaining contract?
A: Subscription upgrades are handled through a contract amendment. You would pay the difference between your current package and the upgraded package.
If you have more questions or would like to talk to us about the new Packages and Pricing, then contact us and we’ll give you more information.
Looking to make some major advances in innovation and digital transformation at your company? Check out how PTC Creo is the leading 3D CAD software in the industry.
I’ll start off explaining to you what exactly PTC Creo Parametric is and what it does for your design process.
What is PTC Creo Parametric?
PTC developed a premium parametric and direct computer-aided design (CAD) modeling software called Pro/ENGINEER. Pro/E was rebranded into PTC Creo Parametric and is now the leading product design software in the product development industry. Over 12,000 manufacturing companies worldwide use PTC Creo (Pro/E) software.
PTC Creo software gives you the ability to work with and edit data from almost any CAD source without recreating designs due to incompatible data. Creo provides a robust and scalable 3D CAD product design toolset for all different skill-levels of engineers and designers. With Creo CAD software you can quickly create 3D models of any part or assembly and improve existing designs with comprehensive surfacing capabilities.
PTC Creo Parametric provides 3D capabilities such as:
- 3D Part & Assembly Design
- Automatic 2D Drawing Creation
- Parametric & Freestyle Surfacing
- Assembly Management & Performance
- Sheet Metal Design
- Mechanism Design
- Plastic Part Design
- Direct Modeling (Flexible Modeling)
- Additive & Subtractive Manufacturing
- Augmented Reality
- Multi-CAD
- Collaboration
- Piping & Cabling
- Rendering
- Design Exploration
- Fastener Design
- Advanced Framework Design
- Legacy Data Migration
- Human Factors Design
- Core Simulation Capabilities
How to Download PTC Creo
“I’m already using another CAD software. How do I know PTC Creo is right for me?” Chances are you like to ride the bike before you buy it, right? That’s why PTC allows you to try it out before you decide to purchase. Download a free 30-day trial of PTC Creo here.
PTC Creo Parametric Software is constantly improving
Every version of Creo is better than the last! For instance, when Creo 4.0 was released it included capabilities for additive manufacturing, model-based definition (MBD), and smart connected design that allows engineers to leverage 3D modeling to define individual components and product assemblies. With Creo 5.0 building on the previous release, it contains all of Creo 4.0’s functionality and more!
The Intelligent Mini Toolbar: the mini-toolbar gives you access to relevant options while staying focused on the graphics area.
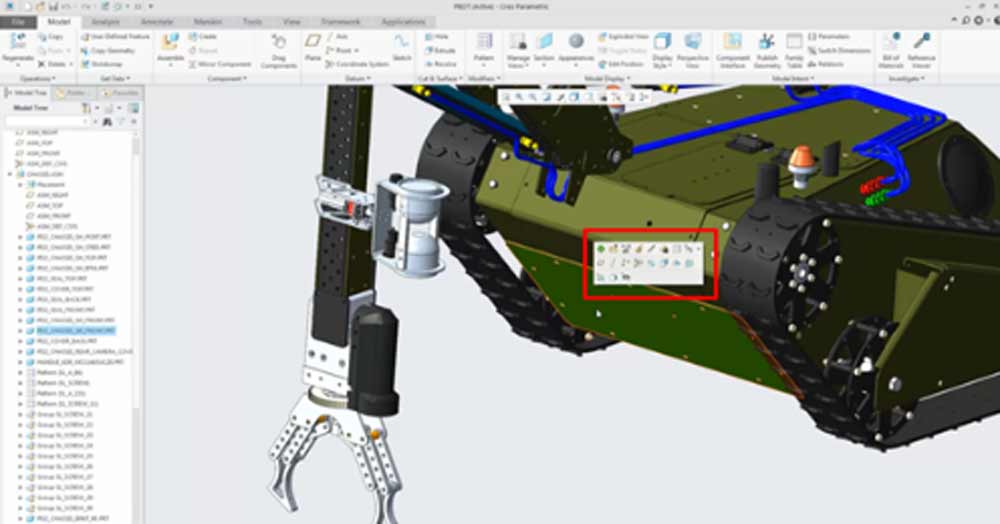
Customizable Menus: you can now tailor the tool for optimal productivity to customize your own workflow.
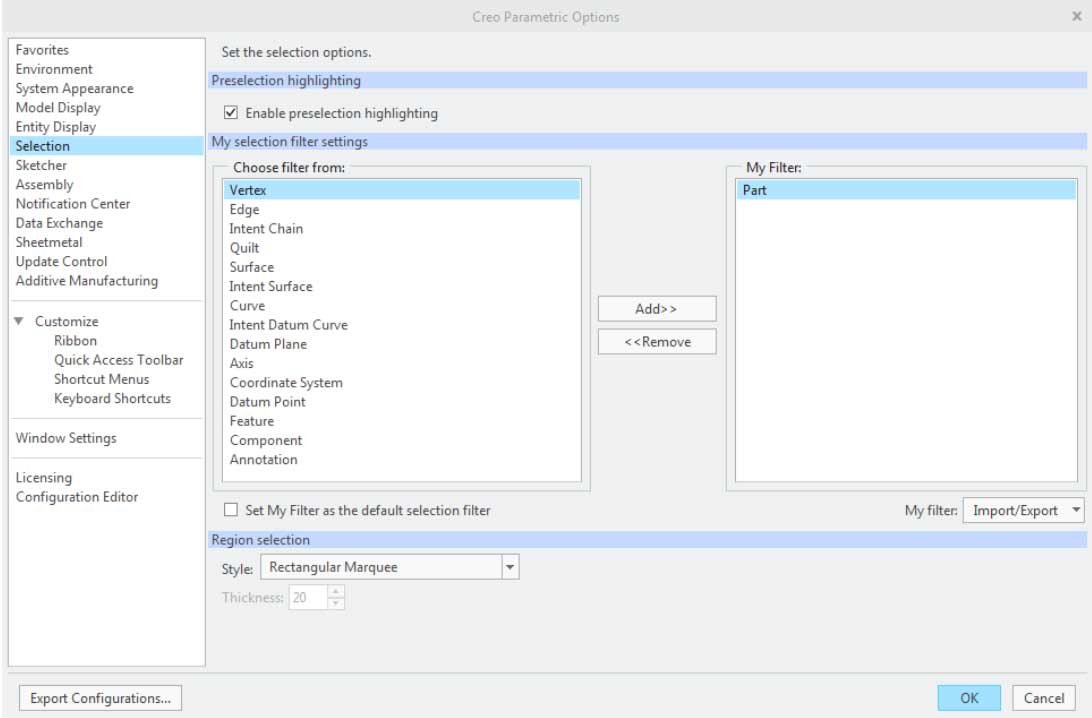
Flexible Modeling for Sheet Metal: you can now edit sheet metal bends, bend reliefs, corner reliefs, corner seams, and forms – simplifying designs for faster analysis.
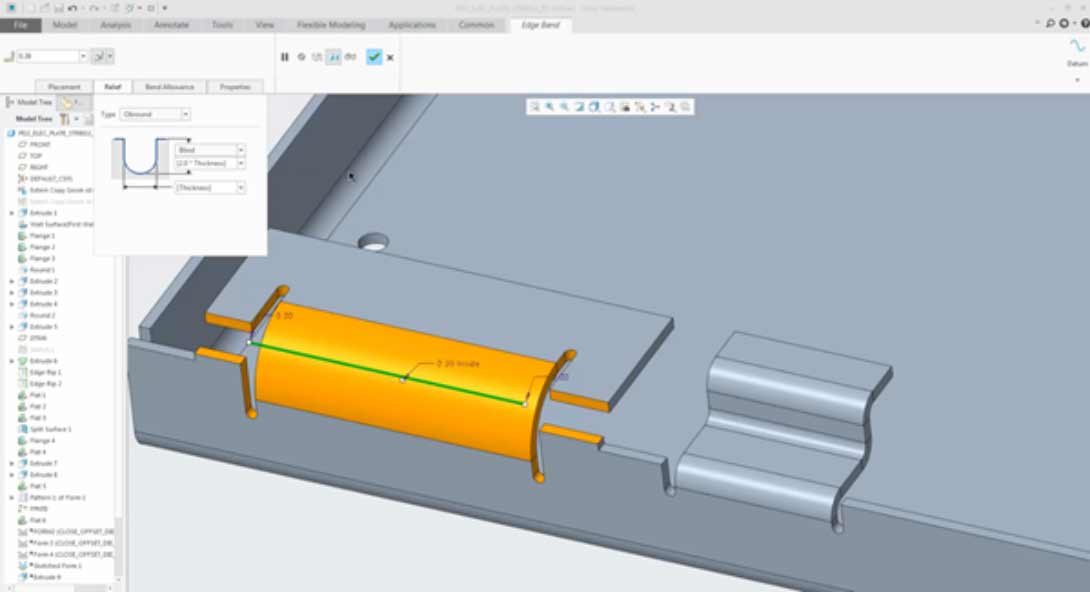
Enhancements to Geometry Manipulation: accessibility to side 2 directly from graphics window when you right-click on a feature without navigating to the dashboard each time; the extrude and revolve tools allow you to specify negative direction values to invert materials for offset geometry; extrude is added to offset to eliminate the step of creating intermediate construction features.
PTC Creo 5.0 includes Topology Optimization, Additive/Subtractive Manufacturing for metal 3D printing, Mold Machining, Flow Analysis, Multi-CAD Collaboration, and improved enhancements with geometry sketch regions, subdivisional modeling, surfacing, sheet metal tools, and volume helical sweeps.
Read more about the newest release in our blog called, “What’s New in Creo 5.0?” or download the data sheet here.
Creo Software – Technology of the Future
When you purchase PTC Creo Software, you have the power to publish, share, and create augmented reality experiences right inside of your 3D CAD models. This allows you to add value to your customer experience because they can now visualize your design with AR.
With Creo Parametric, you also have the power of simulating digital twins within your CAD models to collect real-time data from sensors on a physical product. You can reduce downtime while using this data to find performance issues and schedule predictive maintenance.
As the physical and digital worlds converge, digital transformation starting with the right CAD software is more relevant than ever. PTC Creo software eliminates barriers to innovation and is a solution for product development challenges.
Download a free 30-day trial of PTC Creo to see for yourself how the right CAD software gives you the tools you need to design above and beyond anything you’ve ever imagined.
In a recent Tip of the Week video over on our YouTube channel (https://youtube.com/eacpds) I talked about a new feature in PTC Creo 5.0 – Topology Optimization. Topology optimization has been around for about 20 years, but primarily as stand alone solutions. In spring 2018 PTC announced they had fully embedded a solution from the folks over VR&D into their flagship CAD tool.
This is big news because it allows every user to easily optimize designs in new ways; whether designing for traditional manufacturing or additive manufacturing / 3D printing. Light weighting a part or assembly while maintaining structural integrity is an important part of modern product development. Optimizing topology reduces shipping weight and costs, may improve user experience, and lowers material costs. I’m sure there are other benefits, but those alone can help companies compete in today’s global economy.
After talking with some of our technical resources and engineers, it sounds like the built in Creo 5.0 tool does a fantastic job shrink wrapping/finalizing the optimized geometry to ensure the surfaces can be solidified and don’t have any weird overlapping surfaces or gaps. Most topology optimization tools kick out facetted surfaces that still need to be smoothed out in another tool. Creo turns the optimized geometry into a Creo Freestyle surface that can be easily solidified. This is especially important when optimizing parts for 3D printing.
We’d love to show you this Creo functionality live. So, after you watch the tip of the week video, head over to our contact page to request a demonstration.
The truth is, the small footprint and the simple setup of a 3D printer, such as Formlabs’ Form 2 SLA desktop 3D printer can drastically streamline your design process and impact your business.
Businesses of all sizes have started to realize the need for scalable production and a fast return on investment – eventually turning to desktop 3d printers as a solution.
Desktop 3D printers make high precision 3D printing affordable for everyone, while they deliver a range of operational and business benefits.
Discover the 5 Business benefits of a 3D Desktop Printer.
1. Desktop 3D printers save you money
Desktop 3D printing empowers engineers and product designers to rapidly prototype in-house, saving time and costs at every stage of product development. Here’s how.
For starters, the low upfront costs of 3D printers represent just the tip of the many tangible benefits.
3D desktop printers come at a desktop price and are able to produce industrial quality parts. This allows the development of high-resolution prints for a fraction of the cost of traditional manufacturing.
A desktop printer can pay for itself by printing things or parts you would ordinarily outsource. This cuts out any potential outsourcing fees or shipping costs you might incur.
3D desktop printers also enable the ability to test parts for a device before mass production – quickly. This reduces the costs and risks associated with reworking a design and increases innovation.
You can also save money on material costs by using a 3d desktop printer. Desktop printers use raw materials that can be recycled and re-used in more than one build. Why not make the most out of the materials you paid for?
Affordable materials and accessible machine prices make 3D desktop printers a cost-effective and scalable digital solution for many businesses.
2. Desktop 3D printers save time
One of the greatest benefits of having a desktop 3D printer is speed.
Forget all the obstacles that come along with needing a replacement part from a backed-up manufacture. If you need a part you can create it. It’s that simple.
And if you already have a full sized industrial 3D printer… Well, that’s even better.
Desktop 3D printers can create custom fixtures, tools, and prototypes in a fraction of the time and cost of traditional methods. Why not boost your efficiency and manage multiple machines at once?!
3D desktop printers are designed to quickly integrate 3D printing into your workflow with a range of different materials.
3. Desktop 3D printers help design
With a 3D Desktop printer, you can rapidly develop, evaluate, and iterate a range of designs in-house.
This allows designers to have greater control over the final product.
For instance, additive manufacturing places a model in the hands of the designer in just a few hours.
This allows the designer to be able to continuously improve products and respond quickly and effectively to issues, perhaps by using jigs and fixtures.
3D Desktop printers also provide designers with design freedom.
Design freedom enables a team to quickly create, perfect, and optimize parts with complex geometries.
In fact, you could create small-batch runs or one-off custom solutions for comprehensive field and in-house testing before investing in expensive tooling for production.
By using 3D desktop printer, designers are able to entirely control and rapidly manipulate design.
4. Desktop 3D printers keep all engineering assets in-house
You work hard to keep your trade secrets, so why put any of them at risk.
By controlling all your engineering assets and keeping every process in-house you will reduce your risk.
Using an in-house 3d printer allows you to maintain control over your manufacturing process from beginning to end.
5. Desktop 3D printers don’t need specialized operators
3D Desktop printers don’t require any skilled machinists or machine operators during the building phase.
In fact, the machines follow a completely automated process to print parts. Therefore, anyone that can press a start button can manage the process.
Just imagine the ability to create exhibition-quality parts, in a range of materials with specific properties, with an easy to use machine.
Check out the most affordable, high-precision SLA 3D desktop printer on the market – the Form 2 by Formlabs… Or better yet.. request a free sample.
We’re excited to announce two new additions to the Formlabs SLA printer hardware family. Formlabs is completing the Form 2 SLA workflow with the Form Wash and the Form Cure. These affordable additions to your print finishing area will simplify the isopropyl wash process and ensure consistent part curing. So, what are the Form Wash and Form Cure? I’m glad you asked. Below you’ll see an overview. They are expected to ship fall of ’17.
Formlabs Form Wash and Form Cure
The Form Wash and Form Cure are built to complete the stereolithography (SLA) engine and streamline your 3D printing process to product better results with less time and effort.
Here’s the skinny…
Form Wash Automated Cleaning
- Consistently Clean: Form Wash’s rotating impeller agitates isopropyl alcohol (IPA) around every nook and cranny of your parts, getting them perfectly clean–every time.
- Built to Fit the Build Platform: Parts travel straight from the Form 2 to Form Wash; they can stay right on the build platform or be placed in the basket.
- Automated Wash Cycle: Manual washing requires careful attention, as parts left too long in IPA can become warped/deformed. Form Wash automatically raises parts out of IPA when wash time is up. Parts air dry and are ready when you are.
- IPA Calibration: Form Wash can hold up to 8.6 L liters of IPA, enough to wash approximately 70 prints. The hydrometer lets you know when it’s time to change out IPA. A siphon makes it easy to transfer IPA in and out of the wash bucket.
Maximum Mechanical Properties with Form Cure
- Advanced Heating: Precise heat control is the key to successful post-curing. Form Cure’s chamber is able to achieve temperatures of up to 80 C.
- Balanced UV Light: 13 LEDs use 405 nm Light to trigger the post-curing reaction, working with the heater to post-cure parts.
- Uniform Exposure: A rotating turntable, heat flow, and dispersed lights provide uniform exposure during post-curing.
- An Intuitive Interface: It’s easy to set Form Cure’s temperature and post-cure time. For Standard Resins, simply use the default. For all other materials, use recommended settings for optimum performance.
We are now accepting preorders for both the Form Wash and Form Cure. They are projected to begin shipping this fall. Complete our pre-order form and we’ll get in touch with you to make sure you are in the delivery queue when they start to roll off the dock.
Learn more about the Form 2 SLA 3D desktop printer or request a free sample to see the quality of prints.
Our friends at Formlabs recently announced their newest dental resins to add a range of new capabilities to Formlabs printers, including crown and bridge models, splints, retainers, and soon dentures.
If you walk into a dental lab or clinic today, and you’ll find a completely different set of tools than you would have just few years ago. Dentistry is well on its way to fully embracing digital workflows, replacing messy alginate impressions with digital scans and complicated manual techniques with computer-aided manufacturing.
This should come as no surprise. Every set of teeth is unique, meaning that every dental appliance has to be custom-made. The need for mass customization, and the small size of the final products, makes this a perfect application for 3D printing. While material properties were a barrier to broader application of this technology, new biocompatible materials are enabling dentists to 3D print a growing range of products.
To date, Formlabs dental users have completed over 150,000 prints. Today, with the launch of two new Dental Resins, Formlabs is greatly expanding the range of dental products that the Form 2 can produce. With prints every bit as accurate as larger machines that cost $75,000 or more, the Form 2 is increasingly the go-to 3D printer for the dental professionals.
Use Case
Matt Roberts, CDT, talks about his experience running 4 Form 2 3D printers for various applications in his dental lab here: The Future of Dental 3D Printing, with Matt Roberts from CMR Dental Lab.
Meet the New Resins
Dental Model Resin
Dental Model Resin is designed for crown and bridge models with removable dies, it is a high precision, high accuracy resin. It prints crisp margins and contacts within ± 35 microns and removable dies with a consistently tight fit. It has a smooth, matte surface finish and color similar to gypsum make it easy to switch from analog to digital model production.
Dental LT Clear Resin
A Class IIa biocompatible resin, Dental LT Clear’s high resistance to fracture and wear make it ideal for splints, retainers, and other direct-printed orthodontic devices. This clear material polishes to high optical transparency for beautiful final products.
3D Printed Dentures
We’re pushing the boundaries of digital dentistry and developing the first integrated, end-to-end workflow for manufacturing high-quality 3D printed dentures. Clinical studies and workflow tests are currently in development at Formlabs and partner dental labs, with the new biocompatible Denture Base and Teeth Resins coming in fall 2017.