- Windchill PDM Essentials
- Windchill PDMLink
- Windchill ProjectLink
- Windchill PartsLink
Let’s talk about ERP and PLM, the differences, the benefits and everything you need to know in order to be successful.
Our most popular blog throughout the years has been a defining article of what the differences are between ERP, MRP, and PLM. If you want a high and fast overview of the terms read our previous blog, “ERP/MRP/PLM” – or keep on reading below for a more in-depth look at ERP vs PLM.
Oftentimes organizations wonder: Do you really need both a PLM and an ERP system? Should you, or can you, use just one enterprise system to manage all of your product information? Which system is best? An ERP (enterprise resource planning) system or a PLM (product lifecycle management) system?
We hear these questions all the time.
This article breaks down the similarities as well as the differences between ERP and PLM so you can make the best and most informed decision for your specific situation.
As an organization, it is in your best interest to use technology as a competitive advantage – therefore it’s important to understand the ins and outs of both systems.
With everyone needing to get products to market faster and more efficiently, it’s good to understand that building and sustaining brand equity is just as important as speed to market.
As your company searches for technology that will give you a competitive edge, it’s crucial that you choose the right technology to serve as the foundation for your digital transformation initiatives.
This means choosing technology that will boost your innovation efforts, fulfill your operational and strategic business goals, and help you get closer to your end customers.
While your company continuously faces tough decisions when it comes to technology investments, you may be wondering if it is better to go all-in on an ERP system or invest in a PLM solution.
After all, both ERP and PLM vendors ‘claim’ they can manage both Bill of Materials (BoMs), costs, changes, and other information related to products.
My goal is to help you learn what system or systems are best for your organization.
What is ERP and how does it work?
First, let’s breakdown what ERP is and its benefits.
ERP stands for Enterprise Resource Planning systems, software, and solutions.
One of the biggest driving factors for an enterprise-class ERP system revolves around finance and accounting. ERP systems are important because they ensure your quality products are manufactured in a timely, cost controlled manner once they have been engineered and approved.
This could be why approximately 97 percent of mid-sized companies already use an ERP application.
It’s important to also take into account that ERP solutions are considered to be one of the first software solutions to be categorized as an essential business tool. This could also be why so many organizations are already familiar with ERP.
Although there are many ERP software solutions on the market today, systems you may be familiar with might include Oracle ERP, SAP, Epicor ERP, Microsoft Dynamics AX, and a variety of others.
The fact is, ERP systems are generally built to satisfy the needs of business operations.
This means they are often used for manufacturing (such as manufacturing resource planning), human resources (HR), finance, accounting, purchasing, inventory management, order management, distribution, labor, customer service, and more.
An ERP system can take a product to market and is known for handling operational concerns such as logistics, warehousing, and inventory management.
These systems also provide vast amounts of transactional data which can be used to gauge your financial position and make informed choices about future business decisions.
What is PLM and how does it work?
PLM stands for Product Lifecycle Management software, systems, and solutions.
While ERP systems take transactional units to market, the data and information these systems use should originate in PLM.
PLM is all about the management of the process behind the product, as well as the history and collaboration that goes along with it.
Some PLM systems you may be familiar with include SAP PLM, PTC Windchill, Area PLM, Teamcenter, Siemens PLM, and more.
By adopting PLM software you can reap many rewards.
PLM solutions allow anyone involved in design, development, and manufacturing to work collaboratively with one set of comprehensive, accurate, up-to-date information.
PLM software works by supporting processes that define your brand, engage your customers, and differentiate your company’s products in the marketplace.
The unique value of PLM provides is that the software delivers a “single source of truth” about your product to anyone and everyone who has anything to do with product development.
The difference between ERP and PLM
A simple way to think about the differences between ERP and PLM is to focus on what each system was intended for, especially because both of these systems originate from very different foundations.
Product lifecycle management systems focus on planning.
Enterprise resource management systems focus on execution.
To take a deeper dive, the focus for each system influences the key and unique features that the system provides.
PLM is a collaborative planning tool for your products.
The typical users of a PLM system tend to be product designers and engineers who need to work together to figure out what a product looks like and what it should be made of.
Since PLM is about planning everything about your product, it provides capabilities around managing designs, related services, collaboration with red-lining, task management and more.
Most PLM systems even have a PDM (product documents management) system inside of them. This how they often control the history of the intellectual documentation needed to design and manufacture a product.
These systems control and manage everything from CAD (computer aided drafting) files to program, project and change management processes. A PLM system combines all this functionality and integrates it into an overall product lifecycle management process.
This is why PLM solutions have a higher impact on revenue and brand image.
ERP on the other hand is a system focused on making and executing a product. The primary user of an ERP system tends to be people who deal with manufacturing operations.
Since ERP is about execution and fulfillment, it focuses on capturing information around things such as inventory, purchases and more.
While ERP systems focus only on traditional entities such as item masters, bill of materials and dates, PLM solutions encompass all of the iterative, collaborative, and creative processes that make up the vital elements of your product’s lifecycle.
In short, both solutions are vital for a company to develop and make products as efficiently as possible.
How PLM and ERP work together
Despite sometimes being viewed as competing solutions, ERP and PLM systems work very well together.
In fact, these enterprise systems complement each other, and it is in your benefit to have both! We can help you work through a Return on Investment (ROI) analysis if you’d like. Just contact us.
So how do enterprise resource planning and product lifecycle management systems work together?
PLM software provides the single point of product truth used by ERP to manage product resources and financials.
For example, by using eBoMs (engineering bill of materials) data from your product lifecycle management system, ERP can accurately generate purchasing and inventory management records, creating a unified management of both your resources and production.
Essentially, ERP systems pick up from PLM solutions and take finalized products forward.
This means that design, development, sampling, fitting, approval, assortment planning and all other activities essential to creating great products have already been signed off by the time your products reach the ERP system.
PLM systems help define, design, and plan your product. PLM integrated to ERP allows the systems to feed relevant BoMs and file components, so your manufacturing teams can efficiently order, make, and ship your products.
In fact, combining these two software solutions has only improved end-to end business performance and has already proven to be necessary. This is why so many ERP providers have started to acquire and develop their own PLM platforms!
By using ERP and PLM together, your organization can create a powerful source of data, information, processes and workflows. It can make it easier to create and deliver products from idea generation through design to manufacturing and distribution.
Now that you have a better understanding about how PLM and ERP solutions can positively affect the profitability of your entire company, you are in a better position to understand why it is best to invest and integrate both solutions.
PLM ERP integration benefits
Oftentimes, PLM only gets associated with engineering. In fact, many people don’t even realize that the full product lifecycle management system can integrate with ERP.
Rather than considering whether or not a PLM system could complement an ERP system, you should focus on the benefits your organization will gain by integrating the two.
When used together, your organization will have unified control over your manufacturing process and here’s why.
Today, in order to stay ahead of competition it is essential to deliver the right product, on time, and under budget.
To meet these requirements your organization must shorten design time and product engineering cycles.
By using PLM and ERP systems together, you will increase collaboration throughout your entire organization. ERP and PLM work best together as they collaborate and facilitate movement throughout your organization.
Without PLM, your ERP system is likely to consume and manage inaccurate data from design and engineering. This in turn is likely to deliver minimal (if any) improvements to your business.
Only using an ERP system without a complementary PLM system puts your organization at risk of mismanagement of product changes – which could lead to instances of inaccurate financial planning.
Together, PLM and ERP enhance collaboration between engineers, operations, and suppliers as they provide a single source of product truth. This will help you to seamlessly deliver products from design concept through manufacturing and distribution.
Because these two solutions both focus on products, they help create one single version of your product truth. This helps reduce errors and guarantees that your product documents and product versions are under control.
Seamless PLM to ERP integration will enable your organization to be more agile and reactive in all business activities including traceability, cost, delivery, quality, innovation and more. It helps ease your manufacturing process and creates a more cohesive environment.
By integrating both PLM and ERP, your organization will accelerate innovation, increase productivity, improve quality, and boost your overall performance.
Our Solution: Windchill PLM System
PTC Windchill is our PLM solution that we offer to our customers – so for the 97% of you that already have an ERP system, you should consider complementing it with Windchill. A popular blog called, “What is Windchill?” distinguishes all the ins and outs of this system.
Customer Testimonial:
“Windchill and our new ERP system make it very easy to manage customizations and helps us to make sure that we have materials in-stock and on-time to meet those needs. We save about four hours per job with just the front-end BoM load and getting the information into the ERP system – which has been huge for us.” – Myron Pundt, VP of Engineering, ALM Positioners
Watch our video to learn more about ALM Positioners’ success with PTC Windchill
Why is it important to manage your product Bill of Materials (BoM) in a PLM (Product Lifecycle Management)? This is a tough question to answer across the board for every company, but this article breaks down what you need to know.
The level of BoM management in PLM can be dependent on your companies’ products, downstream systems, and product development processes.
With that in mind, here are some general benefits and reasons to manage the creation of your product BoM in PLM.
The benefit of bill of materials management in PLM
PLM in nature is meant to be a tool to help engineering manage their production date while allowing dynamic collaboration and change control throughout the product development cycle.
The data managed in a product lifecycle management system includes CAD and BoM information, as well as additional supporting product information and documentation.
PLM functionality typically allows an organization to store any and all product information in a structured manner. The structured manner is what properly represents the product within all stages of the product’s development.
This includes everything from initial design requirements, to manufacturing requirements and process plans, to quality assurance documents- all linked to a single product structure.
This gives you the ability to graphically see a truly complete representation of any and all products managed within the PLM system.
In addition, many of the top PLM systems (such as PTC Windchill) give you the ability to manage different views of a single bill of material.
For instance, you could see the design or engineering view of the structure and all design information needed for that BoM product structure.
You would also have the ability to look at a manufacturing view that has the structure defined in a way to support the best possible manufacturing process, while it also links to any supporting information and work instructions.
Additionally, you could see a service BoM that represents exactly what is on-site or on the hands of a customer, with linked product information specifically related to service or support (such as a service repair or product manual).
These systems focus on tracking and managing all cost and profit throughout the process.
Because of this, changes are tightly controlled and require significant steps to ensure proper applications across the system.
There are also few systems that allow for full product representation inside of ERP or MES as outlined above. Nor do they fully support many different views of the same BoM.
ERP tends to only manage what is required to properly manufacture or sell a product, which does not always represent the full product design or its full breadth of supporting information and documentation.
There many impacts on these fundamental differences.
When to use PLM for BoM Management
Here are some general concepts as to when to use PLM for BoM management.
When your product development is in the dynamic phases that require many changes and updates at each phase gate, your bill of materials should be primarily managed in PLM.
If your product requires specific requirements management, detailed manufacturing, quality work instructions, or an intensive manufacturing process, it’s in your best interest to use product lifecycle management for your BoM.
At the very least, all of your product information should also be managed, or linked to your product lifecycle management system to ensure full accountability to all information updates required in the instance of change.
Integrating ERP and PLM
At a minimum, if you have an ERP system it’s important to integrate your system together with PLM.
It’s essential to establish key integration points between your enterprise systems that send needed information back and forth to your enterprise resource planning solution. This will help you properly execute new product releases and changes.
By integrating your systems, your ERP processes will ensure all proper tasks and functions are executed in your ERP or MES systems.
From there, your ERP to PLM system integration would send information back to your PLM system to close the loop.
These are our best practices to help you get ahead and to take product data further. We would love to hear about your thoughts about this topic and answer any additional questions you might have. Feel free to drop a comment below or leave an inquiry under let’s talk.
Looking for an easy way to quickly assess your bill of materials and ensure projects stay on-time and on-track?
These days product data is everywhere. Everyone seems to collect it, have a lot of it, but the question remains; how exactly can you ensure your organization’s product data is being put to good use?
It’s time to take your product development one step further by providing role-based data access, connecting your enterprise systems, and learning how to make the most of your product data. I am going to explain exactly how easy that is to do.
The current state of product data
Companies today have many different roles that require access to product data. This may include people outside of the typical roles of which you may be thinking.
Departments such as engineering, manufacturing, that’s a given, but expand your thinking to include operations, purchasing, and marketing. They all need data access in order to edit and consume information. Think about sourcing…I’ll stop there, but you get the idea.
Let’s focus on the engineering department for a moment.
People could be involved from the mechanical side, the electrical side, or even a quality standpoint. Beyond that, people need to either contribute or consume information that could include manufacturing, service, sales, and more.
Product data game-changers
Product data silos limit productivity – PTC & EAC have the answer.
PTC ThingWorx Navigate was designed to address data accessibility problems by providing simple role-based apps that deliver just the right information to different groups (or departments) in the way that they need
When non-engineering colleagues need access to vital information, they typically interrupt an engineer or designer with a request. ThingWorx Navigate eliminates that distraction and “double-billing.” Through role or task-based self-service applications, data can be securely shared with a team. That way non-expert teams can use a simplified user interface to access the product data they need, right when they need it.
To help accelerate product development processes and take product data even further, our company (EAC Product Development Solutions) has also created what we call EAC Productivity Apps that work alongside ThingWorx Navigate apps.
So what’s the difference between ThingWorx, ThingWorx Navigate and our EAC Productivity apps?
This is a great question- I am going to try and paint the picture for you.
First, it’s important that you understand what ThingWorx is and how it is different from ThingWorx Navigate.
ThingWorx is the proper name of PTC’s Internet of Things (IoT) platform comprised of 5 components; foundation, industrial connectivity, analytics, studio,
The foundation component is the heart of the ThingWorx loT platform used to make connections to ‘things’ which could be machines, products or software systems or pretty much anything with an IP address and a communications interface.
User interfaces to the data coming from these connections are displayed on websites called ‘mashups,’ created with ThingWorx foundation. You might know these perhaps as ‘data mashups’ or possibly as ‘data dashboards’. Simply put, Thingworx is the IoT platform that makes everything possible. (Here’s exactly what makes Thingworx the leading technology for industrial IoT)
Then you have ThingWorx Navigate.
ThingWorx Navigate is the proper name of PTC’s applications that
ThingWorx Navigate Apps use a Windchill (PLM) connector to extract product data for presentation to Windchill Product Lifecycle Management users.
Fundamentally, ThingWorx Navigate Apps are all simply data and product information mashups created with ThingWorx. With ThingWorx Navigate you receive out-of-the-box apps that are instantly ready to be used with your PLM system. The idea behind these product lifecycle management apps is to ensure users can capture the complete functionality of their PLM (product lifecycle management) investment.
ThingWorx Navigate PLM Apps include:
View Design Files – A design file would be a format of a file that isn’t the native CAD format. This could be a staph or Induce or perhaps a 3D PDF
View Drawing – Allows you to look at just drawings. This application pulls drawings from your Windchill PLM system.
View Part Properties – This feature allows you to look at part properties- as if you were hitting the ‘Information button’ next to a file.
View Parts List – Allows you to look at bills of Materials (BOMs)
View Part Structure– With the View Part Structure App, ThingWorx is actually going into PDMLink and showing different aspects of a specific part instead of different ways of going at it (such as having to open several different tabs to get information). Using this application, you can get all your information together on one page. This feature also includes capabilities that cross-highlight part structures within your product. For instance, you could select a component and it would highlight that part and create a hyperlink that allows you to directly look at that specific part. This feature essentially creates a mash-up that takes information from different places inside of Windchill PDMLink and brings them together putting them on one screen, allowing you to have all your information at your fingertips.
View Document & View Document Structure
If you would like to learn more about ThingWorx Navigate technology or if you have any questions, you can always request to talk with Thingworx Navigate specialists here.
PLM Applications created by EAC
Our EAC Productivity Apps (also known as product lifecycle applications)
They allow departments to access content and perform common tasks through a very simple interface, versus having to use a complex product lifecycle management system (PLM) or Enterprise Resource Planning (ERP) system.
PTC Navigate Apps vs. EAC Productivity Apps
Our EAC Productivity Apps provide capabilities beyond that of the out of the box ThingWorx Navigate apps.
In short, ThingWorx Navigate applications allow you to securely access and present role-specific data from your Windchill system. They provide all of the power of a Product Lifecycle Management (PLM) system to someone who is not familiar with its ins-and-outs of product data management.
EAC Productivity Apps take it a step further by taking the underlying technology of ThingWorx Navigate, and the ability to get at the information in the PLM system and create even more complete applications that really give individuals instantaneous access to the information and product data they need to do their job. EAC’s PLM applications are created using PTC’s ThingWorx IoT platform, however, they can run independently of ThingWorx Navigate.
These apps are unique to EAC.
While built using the same ThingWorx foundation, ADK and [Windchill connector], they have their own look, feel and functionality. These mashups are packaged and sold together as a collection. EAC Productivity Apps created for Windchill promote user adoption and amplify the return on the investment you’ve made in your Windchill system, as well as extending role-based visibility into relevant product data and the impact PLM has on your organization.
Take your product data further with EAC Productivity Apps
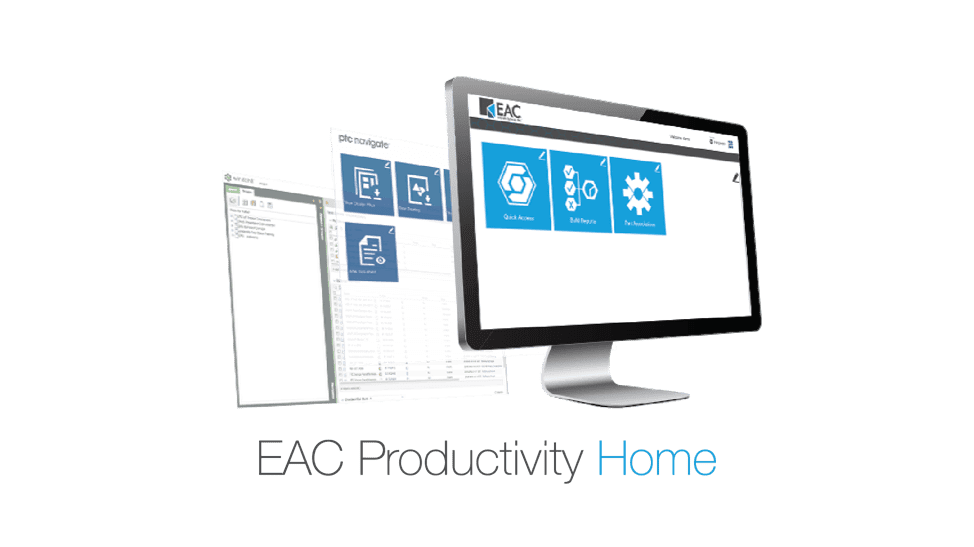
Every subscription of EAC Productivity Apps includes free access to EAC Productivity Home. EAC Productivity Home is a proprietary framework, or launcher, for ThingWorx Navigate applications.
It sits on top of Windchill and
The EAC Productivity App, Quick Search, provides a simple way for users to find content in Windchill. It removes the need for users to apply an understanding of how Windchill objects are related in order to find the information needed to do their job.
The Quick Search PLM application also allows users to search for components and retrieve information and file formats. For instance, if you were to grab a drive system and do a quick search, it’s going to find product information such as parts, EMP like documents, CAD files and more. See EAC Productivity Application Quick Search in action here.
You can also learn more about the Quick Search features in this brochure.
The Quick Access EAC Productivity Application streamlines access to critical and select data sets. Simplifies downstream users feeding critical quality information back to engineering with minimal effort.
This EAC Productivity App allows downstream users to feed critical quality information back to engineering with minimal effort. The simplified interface and consolidated task workflows help users easily submit new problem reports, new change requests, and new variances.
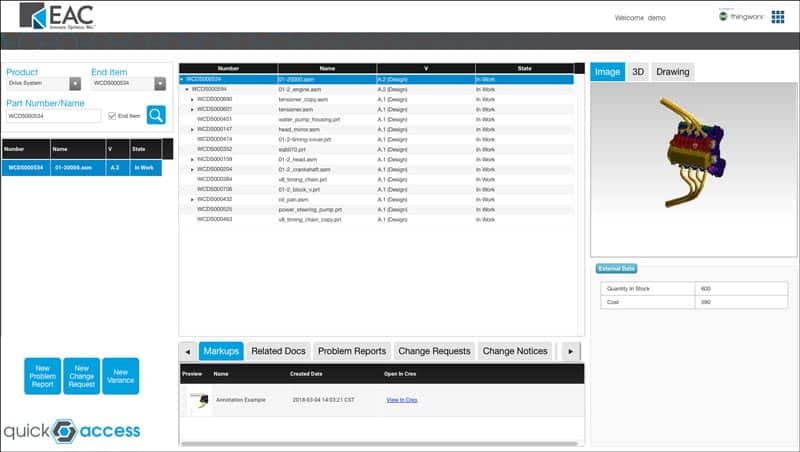
For instance, you could select a component (such as a product), pick its name (the end item number), search for it, and you would get straight to assemblies. With the use of Quick Access users can easily submit new problem reports, change requests, variances and more.
You can learn more about Quick Access features in this brochure.
The Part Associations EAC application provides a “shortcut” for non-CAD users to access critical files and documentation associated with designs like drawings, parts, assemblies, and other documents associated with CAD files and part data.
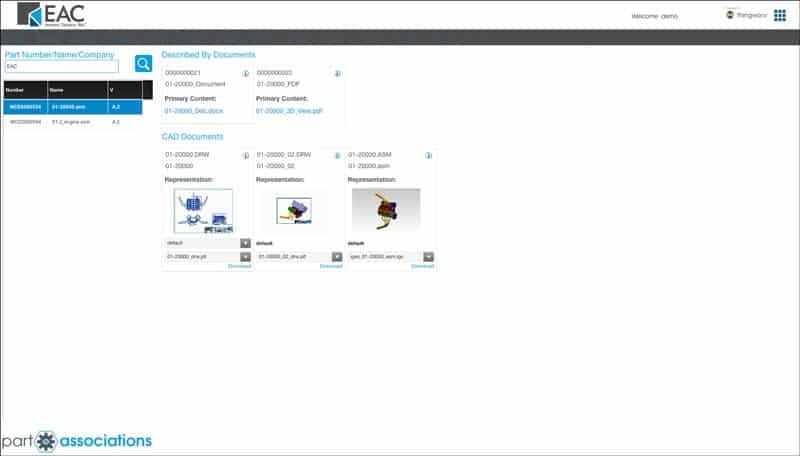
You can learn more about Part Association features in this brochure.
BoM Reports App provides a visual representation of cost
This EAC Productivity App allows users to quickly assess a Bill of Material and ensure projects stay on-time and on-track. The simplified view helps ensure products are built with the appropriate design iterations. With the use of BoM Reports users can easily see BoMs, lists of unreleased parts, parts that have been created or modified by specific users and more.
This app allows users to see the progress of a bill of materials, and apply filters to focus on parts that are not yet released. It is also useful for viewing all of the “make” parts or “buy” parts in a given BoM, or all parts created/modified by a particular user.
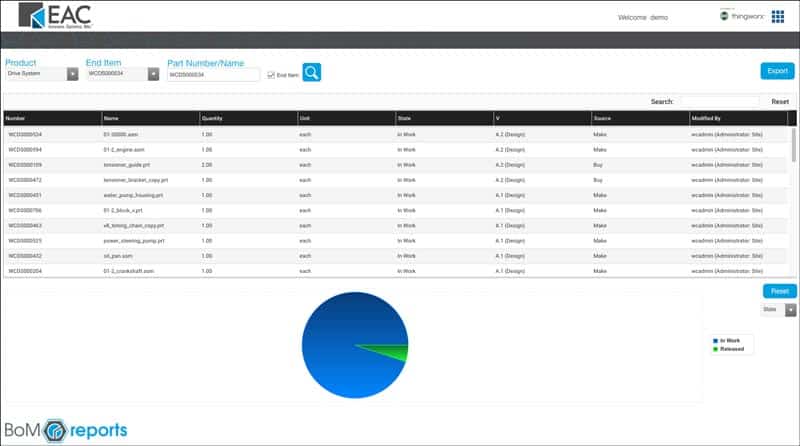
Get better access to your product data
See all the features of EAC P
What are PLM Apps?
Product Lifecycle Management (PLM) Applications (Apps) take data from your product lifecycle management software and combine it with data from your other enterprise solutions to create a single, accessible dashboard view (of all your data), that can be customized for any role within your organization.
Essentially, PLM Apps offer a comprehensive, basic IoT scheme to connect to your equipment, collect data, begin data/alert/notification workflows, deliver role-based dashboards, and more.
Here are four ways that PLM system applications could benefit your business.
PLM Apps, Systems, and more
Odds are, if your business is currently involved with the creation or production of any sort of product, you have likely heard of (or you might already be incorporating) product lifecycle management practices within your business. For those of you who are newer to the concept, product lifecycle management (PLM) often involves implementing software solutions referred to as product lifecycle management software, or systems.
Product management software systems (such as PTC Windchill, SAP PLM, Oracle Agile PLM, Teamcenter PLM, Autodesk Vault, Centric Software, Aras, etc.) are designed to manage your product’s entire lifecycle from ideation through engineering, design, manufacturing, service, and even the disposal of your manufactured products. Oftentimes, PLM software systems are implemented with the intention to integrate product data with other business processes such as manufacturing execution systems (MES), enterprise resource planning (ERP) systems and many other enterprise solutions. However, the reality turns out to be much more complex.
PLM systems are complicated. These systems are complex due to their sophistication and immense capabilities.
In fact, due to the intricacy built within PLM, many companies commonly face challenges with PLM solution interfaces, features, integrations, data sharing, reporting, navigation, and user adoption. Soon enough the PLM technology lives in a ‘vacuum’. Sales and quality managers who don’t use it daily may find it difficult to use.
Other employees might avoid using the PLM systems entirely, and even those who do access the product lifecycle systems daily may find it challenging to coach others who have minimal exposure to these tools. This is exactly why we hear many companies who are not fully entrenched within their PLM systems claiming, “PLM systems don’t deliver on business requirements” or “PLM functionality you expect doesn’t work”.
The reality is – people and departments cannot perform their tasks in isolation. This is exactly where PLM apps add value to your business and streamline workflows.
1. PLM Apps promote cross functional alignment
Traditionally, functional areas within our businesses such as sales, marketing, finance, and operations specialize in different portions of organizational planning activities, which result in conflicts over expectations, preferences, and priorities.
Think about it for a second.
Organizations tend to have isolated departments focused on different business objectives. They often use different data collection systems to accomplish unique tasks. While organizations may consider their teams to be functional, they may fail to recognize the efficiencies they could drive with full cross-functional alignment between and across teams. That or the cross-functional alignment that organizations initially targeted with product lifecycle management didn’t work out as well intended.
This is just one of the reasons PLM Applications are a game-changer. PLM Applications break departmental silos by providing semantic interoperability, ultimately enabling cross-functional alignment.
I know what you’re thinking. “That’s great.. but how exactly does that work?”
Or perhaps, “That’s exactly what I was told my PLM software was supposed to do” just came to mind. The reality is – PLM systems are completely capable of doing everything you had purchased them for, but training everyone in these complex systems is more than a chore. PLM Apps take the foundational features and functionality of your PLM systems and make them easy.
The biggest advantage of these applications is that they actually motivate your siloed departments to utilize the technology investments you’ve already made. PLM Applications extract data from your existing enterprise software systems (such as ERP, MRP, PLM and more), combine that integrated data into easy-to-use interfaces, and enable role-based data access to any user who needs it.
Check out a real-life example of how a fast-moving apparel industry made the product development process exponentially faster and more efficient with the use of mobile apps.
For example, purchasing departments spend most of their time within Enterprise Resource Planning (ERP) systems creating purchase orders, checking stock levels, scrap/rework, etc. They commonly face challenges retrieving engineering data (such as PDF’s, DXF’sand IGES) that are contained in systems controlled by engineering or IT. PLM system applications create self-serve user-based environments that integrate combined enterprise data into consumable interfaces for any end-user or role.
Essentially, PLM applications build user interfaces that non-technical staff can actually understand. PLM Apps can also act as an extension to your existing engineering system, allowing your departments to retrieve drawings without having to ask or burden an engineer. In fact, PLM application interfaces can even be adjusted to display key purchasing information. They have the ability to retrieve all documents (such as PDF’s, DXF’s, IGES, and more) that are associated with a specific order or drawing file.
Creating a self-service business environment for your departments allows purchasing to retrieve the correct drawings (PDF, DXF, IGES) without having to rely on engineering or configuration management.
This is just a few of the ways that PLM engineering applications can enable cross-functional alignment throughout your organization.
2. PLM Applications simplify communication among distributed teams
Forget the need to run around and collect information from multiple departments in order to collect the data a business division needs to do its job. The infrastructure within PLM Apps allows for access/permission controls and change management.
This means you no longer will need to disrupt other departments or coordinate schedules just to exchange information. Plus, by providing everyone with instant access to relevant and up-to-date product information all teams will be on the same page.
3. PLM Apps optimize all aspects of the manufacturing process
Once your siloed teams start to align, the communication between distributed departments becomes more efficient. Your business will be well on its way to optimizing your overall performance. By centralizing all aspects of your product data, your organization will notice relevant common grounds and establish open communications about areas for continuous improvement.
PLM Applications make it easier to view and understand product data within one simple interface gather information from many systems; ultimately enabling your teams and your organization to make better and faster decisions.
Your team’s alignment and enhanced communication will create opportunities for action and better execution. Being able to access accurate data helps everyone maximize output, reduce costs, increase product quality, and get products to market faster.With actions that lead to better execution, your organization will see more success.
4. PLM Apps drive accurate data
According to the Harvard Business Review, workers waste approximately 50% of their time locating data, finding and correcting errors, and searching for sources to confirm the accuracy of data.
Can you believe that?! 50 percent! In addition to wasted time; inaccurate data inevitably leads to redundancy and inefficiency.
Let’s put it in perspective.
Essentially, we are talking about approximately half of the time and salary we are paying managers, decision makers, data scientists, and knowledge workers – gone because people have a hard time accessing data. This scenario makes it easy to see how bad data and complicated interfaces can cost an organization big – time, money and possibly reputation. PLM Applications can help protect you from the negative impacts of bad data. PLM applications can help everyone access to one centralized data source – quickly, and easily.
That’s right. One.
By using only one source for data, your information will be easier to maintain and keep clean. You can be sure everyone is accessing data that is accurate, verified, and up-to-date. Besides, let’s not forget, data drives decisions. By using PLM applications to access and collect your data, your organization can be confident that the data you use for your day-to-day operations is data you can trust.
Overall, PLM applications greatly promote cross-functional alignment throughout organizations, eliminate communication complications between distributed teams, optimize performance aspects within manufacturing processes, and centralize data to ensure accuracy. Think PLM applications could improve the way your business operates? Check out how EAC’s custom PLM applications – EAC Productivity Apps – connect all aspects of your organization.
Imagine if you could manage quality, reliability, and risk at every stage of your product’s life cycle. You could reduce costs, speed innovation, and enhance next generation products. PTC’s product lifecycle management (PLM) software, Windchill, lets you do just that.
Want to see an example of how Windchill software is used? See how Virnig Manufacturing uses PTC Windchill to change the way their data is delivered within their organization.
Already using Windchill and need help with admin and support? You’ll want to check out our Alliance Program, provided to our customers for on-going technical support, business process consulting, and mentoring services on a monthly basis.
Already using Windchill but you or some of your team member don’t use it often, therefore, it gets confusing? You’ll want to check out our role-based apps for casual Windchill users – EAC Productivity Apps or ThingWorx Navigate will help you.
Don’t know what the heck PTC Windchill is? Then read on.
What is PTC Windchill?
PTC Windchill is a product lifecycle management (PLM) application suite that leverages a consolidated view of product information through multi-system data. It’s a systemic enterprise wide approach to maintaining product and process quality throughout the entire product lifecycle.
PTC Windchill PLM software provides a complete functionality dimension to help organizations capture product structures from computer-aided design tools, transform them into full engineering bill of materials (eBoMS), to manufacturing bill of materials (mBoMS), to service bill of materials (sBoMS) all while retaining the linkages between different perspectives on the product. Windchill solutions break down organizational barriers, allowing teams to work faster and more accurately all while reducing time-to-market and cutting costs.
The Windchill Product Lifecycle Management system can help streamline your product development and service information processes. It’s a system that can help your organization create better products, with more variations, faster, at a lower cost. As a manufacturer, your pressures are not only continual – they’re mounting. Your industry is changing. Your customers’ requirements are evolving. And your supply chain is constantly adjusting to
Windchill helps with exactly that. As an integral component of PTC ’s Product Development System, Windchill manages all product content and business processes throughout the product and service lifecycle. And it has a robust, high-performing architecture to help you today – and to prepare you for tomorrow’s uncertainties. Windchill provides a rich systematic approach for creating, configuring, managing and reusing product structures and associated content, such as CAD files, documentation, requirements, manufacturing information, service information, part/supplier data, calculations and illustrations.
Windchill can also play an important role in increasing your company’s competitiveness by allowing continuous improvements and automation of business processes and procedures. Windchill is an
PTC Windchill Cost
PTC Windchill made updates to their PLM packaging and pricing – which means you can customize dashboards and product data more than ever before at a cost that makes sense for your organization. Here is a breakdown of the new PLM structure.
PTC Windchill Certification
Once you’re ready to purchase the software, you’ll need to make sure it’s learned and understood in a timely manner and without frustration. We have a few options:
Short-Term Support: EAC’s Product Development System Services Team has a long track record of successfully implementing Windchill products.
Long-Term Support: Check out our Alliance Program – EAC’s PTC Windchill system administration and support services for on-going technical support.
Support at your own pace: Your team can get PTC Windchill certified by taking our classes we offer for end users and managers. Check out our training schedule.
The Windchill Products Explained:
Windchill products are application modules that offer users specific sets of features and capabilities within the Windchill application suite. Some of the most common Windchill PLM modules include:
What is Windchill PDM Essentials?
PTC Windchill Product Data Management (PDM) Essentials is built on PTC’s production proven PTC Windchill software.
Windchill PDM Essentials simplifies data management activities by transparently incorporating them into the design process. It manages all forms of information such as CAD drawings, customer requirements, schematics and Bill of Materials (BoMs) that are generated during product development.
This modern product data management solution makes it easy to manage, share, and review your data. It’s finally possible to have a single view of the latest product data, along with tighter integration to major end CAD vendors, Microsoft Office, and desktop tools. Plus, it allows your users to save time with better version control, automated data release, and simple search capabilities. Learn more by reading the PTC Windchill PDM Essentials Data Sheet.
What is Windchill PDMLink?
With an abundance of data dispersed throughout your organization, how do you maintain the integrity of your product information when multiple people are working on the same files? The solution is easy – Windchill PDMLink.
Windchill PDMLink is a Web-based, industry-proven Product Data Management (PDM) system that supports geographically dispersed teams while managing critical processes such as content, change and configuration management. Windchill PDMLink maintains the integrity of your product information by storing master data in a secure area where you can control, monitor, and record all changes.
When a change is made to your data, Windchill PDMLink stores a modified copy of the data, signed and dated, in a secure area alongside the old data, which remains in its original form as a permanent record. In addition to providing change control management, Windchill PDMLink enables you to manage your product’s release cycle as well as its configuration. Check out the PTC Windchill PDMLink Data Sheet for more information.
What is Windchill ProjectLink?
Windchill ProjectLink is a collaborative product development web-based environment that automates and tracks projects.
ProjectLink provides a common workspace where you and your team can share and discuss documents and product structures, hold meetings, and communicate and track progress on tasks. From private exchange environments to public business to business (B2B) exchanges, ProjectLink is a secure web-based system that can easily be used in any collaboration environment.
It can also be used well beyond the engineering and manufacturing departments of your organization. Any project that requires team members to share electronic information such as writing annual reports to
What is Windchill Partslink?
Windchill PartsLink is a module for PDMLink that adds part classification-based features.
PartsLink enables you to perform parametric attribute searching and manage your results through convenient navigation and searching. You can search parts by typing a free-form product description or a part number in the search criteria text box. You can browse the hierarchically organized structure of your parts using text and images. You can also refine your search by constraining parameters in a parametric search.
Windchill PartsLink enables your team to perform similar part searches, expanding your search to look for matching parts that have parametric attributes that are within a certain percentage or absolute tolerance of the selected part. Additionally, you can export the result set to a file.
Many companies lack a comprehensive part search system and as a result they lose the benefits of reusing product components. Criteria-based searching limits the result set, which helps a great deal in reuse decisions. PTC Windchill PartsLink helps solve that problem.
What is Windchill Quality Solutions?
Depending on your specific Windchill Quality Solutions suite (Windchill Quality Solutions 10.1 Desktop, Windchill Quality Solutions 10.1 Administrator, Windchill Quality Solutions 10.1 Web Access) you may have access to one or more applications.
Windchill Quality Solutions, the desktop version, is the cornerstone of the Windchill Quality Solutions suite. It is available in both the team and enterprise additions and is the feature rich windows application for all of your reliability and maintainability activities.
Available in the enterprise addition you will also find Windchill Quality Solutions Administrator which provides you options for administrative controls including options to support secure login.
Windchill Quality Solutions Web Access available specifically for Windchill FMEA infractions in the enterprise edition, allows you access for data entry, filtering, graphing, reporting and more.
Is there other Windchill Software for product data management and process management?
- Windchill MPMLink acts as an integral solution for Manufacturing Process Management.
- Windchill FlexPLM is a product lifecycle management solution that is widely used for retail, footwear & apparel and consumer product companies.
- Windchill Requirements Management is a combination of PTC’s Integrity product and Windchill PDMLink that manages product data software and hardware requirements.
- Windchill PPMLink is a program that provides portfolio management capabilities to discrete manufacturers.
- Windchill Service Information Manager creates associative, interactive service parts information used throughout a product’s serviceable lifecycle.
- Windchill Service Parts improves service operations by enabling service information to be organized and optimized for accuracy, applicability, and rich, graphics-driven delivery.
Want to see a PTC Windchill tutorial to see the software in action? Watch this on-demand video of Windchill’s basic software capabilities.
Manufacturers always try to find a ways to streamline processes and ‘do more with less.’ It drives success in a world full of competition. One way organizations do this is by reducing process complexity with powerful product life cycle management (PLM) or change management software. Connecting your team directly to live operational data increases efficiency in all departments and allows your organization to save money and manufacture products faster.
EAC Product Development Solutions has partnered with PTC, the world’s product development technology leader, to bring organizations the products and services that they need to succeed in their industry. As a PTC Solutions Provider, we provide the maintenance, support, configuration, and training you need to implement change management software as easily as possible.
PTC Windchill Data Management
If you’re looking to do things like keeping better track of files, create and store Bill of Materials (BoMs), put CAD models and drawings in one place, eliminate the risk of two individuals working on a file at the same time, or secure your data without burdening IT – you’re looking for PTC Windchill.
PTC software – specifically Windchill – is a complete PLM solution that provides capabilities such as:
- Bill of Materials (BoM) Management (EBoM, SBoM, MBoM)
- Configuration and Change Management
- Requirements Capture Management
- Early insight into product quality, reliability, and risk
- Efficiently making product variations with a structured platform
- Product Data Management
- Collaboration across all departments with accurate, up-to-date information
- Seamless software integration and defining standards
PTC Windchill is a PLM solution that provides a smooth transition from design to manufacturing with universal access to all critical product data information so that the process isn’t fatigued with delays.
PTC Windchill, Change Management, eBoM Case Study
ALM Positioners, a leading manufacturer of positioner lifts located in Rock Island Illinois, needed PTC Windchill. The company offers unique, customizable weldments and assemblies that require a lot of CAD models and other product information from engineering before manufacturing even begins. Due to extensive product customization and configuration depending on the needs of their customers, ALM needed a better solution to manage product data. They were drowning in paper files – a lot of which had outdated information.
EAC’s implementation team helped ALM Positioners transition to a digital workflow using PTC’s Windchill software. Windchill helped ALM save up to 4 hours per project by integrating EBoMs and MBoMs into their ERP system.
Watch the ALM Case Study on PTC Windchill to see how it has consistently proven to be a leader in the industry and outperformed competitors when it came to product lifecycle management.