The Form Wash is designed for the Form 2 3D printer from Formlabs to automate the cleaning process between printing parts. It makes things much easier for engineers who don’t want to waste any time cleaning their prototypes so they can either use the Form 2 again for another print job or get back to their next project.
Washing printed parts before post-curing helps to remove excess residual resin from part surfaces and cavities. Formlabs suggests using isopropyl alcohol (IPA) as the solvent that is most compatible with washing.
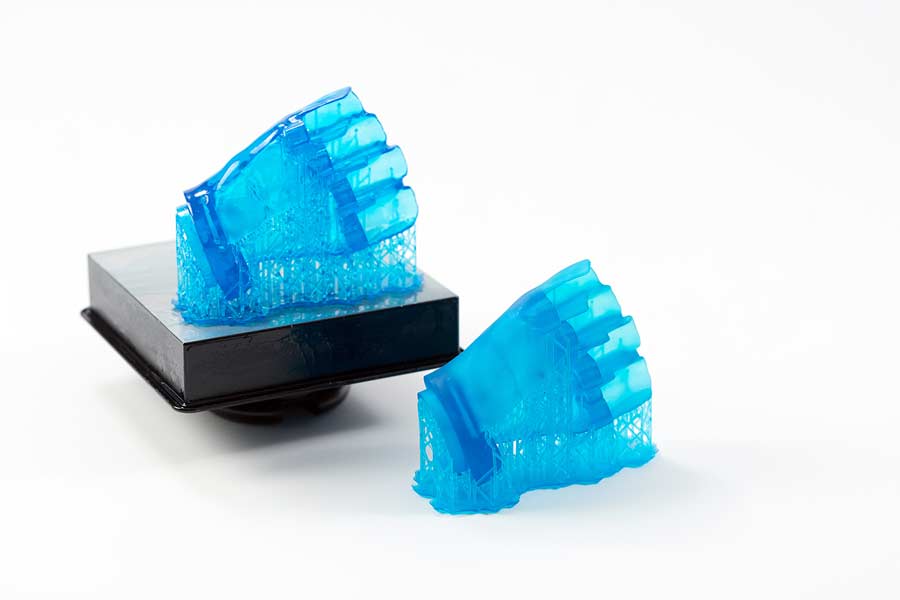
If you take a look at the image above, you can see that the left part is much cleaner and visually is more detailed than its counterpart. After using the Form Wash, you can typically use the Form Cure to expose printed parts to light and heat to stabilize the parts for performance. Using the Form Cure is not necessary but using the Form Wash and Form Cure together is recommended for optimal finishing.
Colder Products Company (CPC) has trusted EAC for years to provide them multiple Form 2 printers and other Formlabs equipment and materials to rapidly prototype customized quick disconnect couplings, fittings, and connectors for plastic tubing used around the globe. We answer a few questions that users have about the Form 2 and also include an engineer’s intake as well. Here is how Jeff Martin, an applications engineer at CPC, uses the Form Wash in-house to reduce time spent cleaning 3D printed parts.
How much time does it take for one wash?
Formlabs says that most resins require washing for the Form Wash default programmed time, which is 10 minutes – although additional time is needed for some resins. The following table shows Formlabs’ recommended wash times for each resin being used.
Resin | Wash Time | Resin | Wash Time |
Tough | 20 min | Elastic | 10 min + 10 min |
Rigid | 15 min | Dental SG | 5 min |
Grey Pro | 15 min | Dental LT Clear | 5 min |
Castable | 10 min | Denture Teeth & Base | 10 min |
Castable Wax | 10 min | Ceramic | 5 min |
High Temp | 6 min | All other resins | 10 min |
Jeff suggests that you should set your wash time at 20 minutes for each wash. He also recommends that it’s best to physically have 2 Form Washes in-house to speed up the cleaning process, “The first Form Wash set to 10 minutes to wash parts hanging from the build platform, and the second Form Wash is used to clean the parts broken free from supports.” (Keep in mind, he typically uses Rigid Resin for his 3D prints).
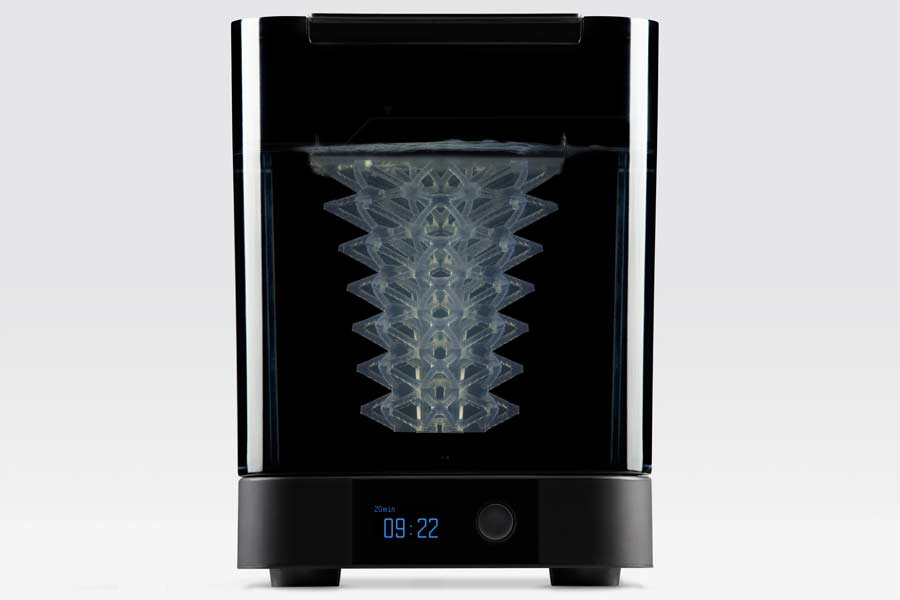
What’s the best way to wash prototypes?
If you’re using the Finishing Kit, Formlabs recommends that you should wash your prototypes in at least two standard wash tanks – the first wash, being the ‘dirty’ wash, would take 10 minutes and then the second wash, using a cleaner tank, for another 10 minutes. Once the first tank gets dirty, you can dispose the IPA, transfer the second tank into the first tank, and then pour new alcohol into the second tank.
The Finishing Kit includes 2 wash tubs to manually clean your 3D prints – whereas the Form Wash automatically cleans your parts and prototypes.
Jeff says the advantage of having a second Form Wash is that you can use Formlabs’ same theory of having a clean tank to do the final rinse. “I find it in my experience to be extremely useful to remove the supports for the second wash. The reason is that the supports block the fresh circulation of clean solvent from the parts. You will notice that for deep aspect bores and blind holes, if you do not remove the supports, they often times will not fully be cleaned of resin. After removing the supports and letting the parts bounce around in the basket during the last 10 minutes, they will always come out clean.”
Learn more FAQ by reading our related blog, “Everything You Need to Know About the Form 2 3D Printer.” If you’re interested in a free sample, then contact us at your earliest convenience.
Also, follow me on LinkedIn for tips and tricks on how to use the Form 2 and other equipment and materials from Formlabs!
Lakeville South High School’s STEM Academy is encouraging students to problem-solve in a whole new way. Kurt Weber switched his role from a biology and chemistry teacher to teaching STEM classes 4 years ago. He says there is no going back. He loves teaching students the curriculum behind the subjects that drive these classes – science, technology, engineering, and mathematics.
Using STEM Education to Remove Unfavorable Learned Behaviors
Weber says that when he caught one of his students on his phone during class, he confronted him. The student replied that he was ‘done’ with his project. Weber says this gave him an opportunity to bring that student around the lab to show him all of the things he could be doing in addition to the project that he had already finished. He explained to the student that learning doesn’t stop once the task is over.
He explained that the kid wasn’t being snarky by saying he was ‘done’ and he didn’t take it that way either. Weber says that every kid has the ability to problem solve at a very young age but that ability is stripped away so fast with traditional learning methods in the classroom.
Weber goes on to say that most kids are conditioned to only do what they are told and nothing more. Following orders and checking things off lists leaves no room for creativity or innovation. No one has really given the students that kind freedom in their learning until the STEM Academy came along and started changing the way students think and approach problems.
To continue learning outside of the realm of what a student is asked to do is what will help that student in real-world situations as an adult.
STEM principles are teaching students how to lead, not follow
“They learn inherently, by failing,” Weber says. “Being in this class gives them an opportunity to solve a problem on their own – and the worst thing they could do is fail. They’re so scared of failing.”
He explained that when rulers were taken away and students were asked to measure a piece of equipment with which were working – they didn’t know what to do and got frustrated. This frustration comes from the fear of failing. Weber then asks the students what else they could use in the room to measure the object? A student came up with the idea of counting the ceiling tiles or using another frame of reference like a book, or a backpack. This is exactly what Weber is looking for. Out-of-the-box ideas. Critical thinking. Solutions that are derived from limited resources.
“We don’t tell them how to do it. We tell them how to get from point A to point B. It changes the way you look at everything in the world.” At this point, the students wanted to learn. They were excited to accomplish a small win and were motivated to keep on going. Weber says that the fear of failure is the norm and we need to combat it. “Failure, in general, is something they try to steer clear of. We need to tell them to lean into failure.”
What does the STEM curriculum look like?
Other class electives were unintentionally eliminated when the STEM classes became available because registration in other classes dropped. What’s so appealing about these classes and why have they become so popular at Lakeville South?
Weber gives his students the freedom to work at their own pace; an opportunity rarely given to students in other classes. Students have to complete 8 semesters of math, 8 semesters of science, Engineering Your Future 1, Engineering Your Future 2, and then get to choose one of the STEM pathways; Computer Programming, Biomedical, Engineering, or Industrial Technologies. To complete the STEM Academy, students complete a capstone project in which they can work with a local business to solve real problems. Weber says that he’s been able to create his own curriculum for the STEM classes and it’s been evolving every year as additional lab equipment, like 3D printers, and technology are made available to his students.
Weber says that there was no need to convince students to join the class. He says that the students bragged enough about their STEM class that there was no need to make additional efforts to gain students’ attention when it was time to choose electives. As far as keeping students’ attention in the STEM classes, Weber says he frequently has to tell students to go home because the school day had already ended hours ago.
How does the STEM Academy benefit students who don’t end up pursuing a career in science, technology, engineering, or mathematics? Weber says that the classes give them confidence in their ability to solve a problem. “They don’t need someone to tell them what to do. They need a mentor.”
Learn more about Lakeville South High School’s STEM Academy here.
EAC Product Development Solutions is passionate about transforming our client’s ideas, needs and challenges into innovative, marketable products that support successful brands — That’s why we created our EAC Design & Engineering Services Team.
Our team consistently works with manufacturers, academic institutions, and engineering and design organizations throughout North America to solve all kinds of engineering challenges.
Finding, selecting, and trusting an outside engineering group is a tall order. We get it. There are a lot of questions people have as they vet potential partners. Here are answers to the top 10 questions people ask about our engineering services. We hope this helps.
1. What engineering services does EAC offer?
Our engineering services team provides mechanical engineering, product design, industrial design, proof of concept, IoT / Smart-Connected design & development, and analysis (FEA) services to help individuals and organizations realize their product ideas and get to market faster.
We are proud to say our engineering team can handle just about any engineering challenge thrown our way. Our complete engineering capabilities include CAD, detailed technical specification product requirements, design validation and optimization, IoT (Internet of Things), smart connected products, manufacturing, FEA (Finite Elements Analysis), simulation, analysis and more.
You can check out our Engineering Services Brochure for specifics on our design and engineering principles, services, manufacturing competencies, and our software competencies.
Still have questions about our engineering services and competencies? You can always send us a message here, and we will be more than happy to personally answer any inquiries you might have.
2. What is the EAC engineering services background?
This is a question we get asked a lot.
We have offered our engineering services for over 21 years and counting. Throughout the course of these years, we have completed over 400 engineering service projects on time and under budget!
It is important to us that you know our engineering services team leverages years of experience and extensive knowledge of industry standards and tools to deliver manufacturable, innovative designs. This is a distinguishing and highly valued characteristic of our company.
3. What is the EAC engineering services project process?
If you have an idea or a project request, our engineering services team will work with you initially at no cost to further scope out your vision. We do this to ensure we have all your proper project requirements and to figure out two things: 1) What you are looking to do and 2) If we are a good fit.
Once we fully understand your engineering project we build out a statement of work. Our statement of work outlines our plan and what we are going to do.
After our statement of work is defined, the team carries out the project delivery under the watchful eye of your dedicated project manager.
Throughout the duration of the project, our team will keep you updated with the daily or weekly status updates. The frequency of the updates is entirely up to you.
No matter the size and the duration of your project, we still use the same project management process for every engineering service project we complete.
4. What are the professional engineering costs?
Our professional engineering costs generally do not vary, but the amount of work we do for customers varies according to the goal. (Keep an eye out for another blog that will dive into this with more detail)
Our engineering team considers the type of project you are looking to complete, the work you need to be done, your project size, your project timeline, and much more.
Because our fees and rates fluctuate due to so many factors, we offer a Free Project Scope to address your specific engineering needs and requirements. This way you can be assured you will get the most accurate engineering project quote. We’re not trying to play our cards close to our chest. We’d legitimately like to talk through your project and provide the best, most accurate quote possible. No strings attached.
5. What similar engineering projects has EAC worked on in the past?
With over 400 engineering projects completed on time and under budget, we have a plethora of project examples to demonstrate our expertise. We’ve worked on everything from consumer products to industrial equipment. We’ve optimized designs for traditional manufacturing, various molding methods, and IoT requirements.
For example, see how our Engineering Services team helped Condux International (Case Study) and Core Distribution (Case Study).
You might also check out how our engineering services team helped Milestone AV Technologies complete a critical project 40% faster.
6. What happens to the intellectual property of my engineering project?
The intellectual property of the engineering services project EAC completes for you is entirely yours. We call this out in our statement of work.
You can think of our engineering services team as your contracted in-house engineers. The rights to everything we do are completely owned by you. If we create something for you, it is entirely owned by you.
At the end of your engineering project we gladly turn over anything and everything we used to create and solve your engineering needs.
7. Can EAC help with fabrication or fabrication partners?
Although we don’t have specific fabrication partners, we are able to help you find companies that can fabricate and produce products for you. Over the years we’ve built a long list of trusted manufacturers.
Whether you are looking for an initial prototype run, a full production run, building only a few products, or you need help transitioning and optimizing your current design for full production—we can help.
Our engineering services team is more than happy to assist you in the process, as well as guide any conversation with the production facility. If you would like our expertise, we’re happy to help.
8. Can the EAC engineers work on-site with our engineering staff?
Our EAC engineering services team can work on-site, but we do have some geographical limitations. Contact us to see if having our EAC engineering services onsite could be an option for you.
9. How many resources can EAC devote to my engineering project?
We have a staff of highly trained and educated engineers, but we are not limited to just that. The resources assigned to any specific project depend on the timelines and tasks defined in the statement of work.
If your engineering project requires additional resources and contractors our team is well equipped (and networked) to work with and manage additional help to complete your project.
10. Does the EAC engineering services team have any references?
Of course. Here are just a few examples of what our customers have had to say about our engineering services:
“EAC was able to decrease the overall weight by nearly half. They did a nice job coming up with innovative solutions to reduce the amount of machining required by the hanging fixture.”
- -Josh Siebert, Engineering Manager, Condux International
“We needed 3D modeling expertise and experience in getting a design to manufacture stage. EAC looked at the mechanics of our product in detail and produced a well-optimized design and high quality drawings.”
- – Eric Wahl, Owner, Colorado Solar Inc.
“The most valuable part of partnering with EAC goes back to having faith very early on that the technical rigor and detail was being addressed. I was assured that the EAC team was going to do the diligence necessary to create a good design because of this.”
– Mike Ardito, Director of Product Development, Milestone AV Technologies
To view other EAC customer testimonials you can always scroll to the bottom of our Design & Engineering Page.
Beyond the typical questions we get asked about our engineering services, we thought it might be beneficial for you to learn the benefits of out outsourcing your projects and how hiring outside engineering help can shorten your time-to-market and give you a competitive edge.
Furthermore, don’t hesitate to contact us about Design & Engineering Services questions.
Here’s why engineering processes affect services and why streamlining information could solve the whole problem.
The Problem: Lack of Communication
Let’s be honest, engineering and manufacturing departments do not always communicate product changes to service. This is just the start of how your engineering processes affect services.
The Result: High Costs
When technicians reference outdated product information and arrive with incorrect parts, this leads to longer service visits, extraneous costs, longer downtime, and lowered customer satisfaction.
The Solution: Streamlining Information
Streamline the way you service teams access and use product information. The best way to accomplish this involves accurately transforming eBOMs (engineering bill of materials) to sBOMs (service bill of materials) and maintaining the fidelity of that information after engineering changes.
It’s time to stop letting your engineering processes affect services.
Take full advantage of the product data your organization has already created.
Structure service manuals and part information based on how a specific product is configured and serviced. Reuse engineering and manufacturing data in the service environment. Provide configuration-specific information to service technicians. Create a single point of access for your service content. Avoid text – use and repurpose graphics, animations, and CAD information when possible. And link service information to engineering information so changes propagate.
Next: Identify Your Service Needs
Identify what should go in your sBOM to ensure your sBOMs meet the needs of the service department. Examples might include what is serviceable versus what is replaceable, the status of a part, the components, models, grouped items, and more.
The Goal: Transforming Your Services
Remember: the ultimate goal is to make your customers happy. As a result of combining best practices with the right technology to support service and parts information management and publication you will see a higher customer satisfaction, improved technician effectiveness, improved brand reputation, higher profitability (due to lower revenue and service cost), time savings, and higher revenue (from repeat business and customer loyalty).
We have a team of technical communications specialists that would love to talk with you about your current state and current initiatives…
From industry experience we know how difficult it is to get projects done by end of year – especially when most manufacturing facilities close on average for two weeks during the holidays. When your company is shut down for the holidays who wants to return to all of that work at the beginning of a new year? Let me answer that for you. You don’t.
Our solution? We would like to gift you more time this season. Time, that is, to not have to work on engineering projects that will push back your project timeline into next year and into next quarter. No, we are not work-aholics. Our CEO gives us our holidays off but we do not do a hard shutdown during the holidays like some manufacturing plants do. And we’d like to see you get a head start on your 2018 year goals.
So what does this mean for you? Less work. We would love to offer our engineering services to you when you need it the most. We know you value your time and you’re eager to enjoy some downtime around the holidays.
Want to learn more about our design and engineering services? Check us out here.
You probably have a checklist for what to do when your company shuts down for a few weeks, but if you need a refresher -here are a few steps.
3 Steps to Take if your Company is Closed During Holidays
If you are shut down for the holidays – here is a short checklist you may want to double check to make sure you’re ready to leave for the holidays.
Notify Employees, Customers, Vendors, and Hospitality Services
Notifying employees may be the obvious one but you can imagine that with everyone finding the time to get everything done by the end of the year – it’s easier to plan your to-do list around the time that you actually have when the office is open. So notify your employees internally via email, calendar, Facebook Workplace, or by another platform you’ve set up for internal communication.
Make sure all of your customers and clients know all of the days that you will be closed. This is especially important for those that are trying to get a hold of your business during office hours when you are typically open. Make sure that you have a personal out-of-the-office voicemail set up in case they didn’t get that email you sent. Think about setting up a calendar or a list of all of the holidays and pre-planned office shutdowns to be available on your website so there is no confusion.
Vendors may have reoccurring delivery schedules that need to be notified via phone, text, or email to put a hold on deliverables. And sometimes it may be easy to forget about your hospitality services that come in the middle of the night once or twice a week to clean your office – don’t make the janitors and clean-up crew come in when you aren’t at the office to make a mess.
Turn off Office Equipment & Turn Down the Thermostat
Don’t just say that your business is green – take actions to preserve energy by turning off all of the office lights, any office machinery that won’t be used, and turning down the thermostat for the shutdown. Not only will you be saving energy – you’ll be saving a lot of money in energy costs too.
Prepare to Start the New Year with a Bang
Your customers are going to want to hear from you at the beginning of a fiscal year. What better way to do that than write a refreshing handwritten card to send when you get back into the office from your holiday retreat? If you don’t have time to do a handwritten card because you have a longer to-do list than expected, then at least send an personal email out that wishes farewell to 2017 and a warm welcome to 2018.
Also, sending a letter out is an opportunity to inform your customers of any upcoming and exciting events or products that will hit the market at the start of the new year. They’ll want to hear about what you’ve got in store for them.
Don’t forget to take advantage of our Design and Engineering Services this holiday season – as we would like to help you get a head start on the new year with your engineering projects.
There are a lot of things in life we as humans seem to put on autopilot. We seem to do things the same way, around the same time, even sometimes in the same place. Despite our best efforts to be different, we find ourselves thinking, behaving, and feeling the same way we did yesterday and the even days, months, and years before that. It’s time to challenge your ways.
Look at the way you do things for instance.
If you’re anything like me, you have routines for almost everything you do, from the time you wake up to the time you go to work. We often get so accustomed to how we do things, finding the reasons why we do them becomes a challenge. It is easy to overlook our other options if we fail to recognize the benefits of change. It is this very mindset that holds us, and the rest of the world from reaching our full potential.
Aside from personally challenging our ways, we should also be challenging our business processes.
It is my belief that companies, more than individuals, tend to do what they’ve always done. We become comfortable in the systems we know, the methods we have created, and the processes we have established. This is when we fail to recognize opportunity in organizational change.
Although the concept of change can be frightening for some the reality is, success doesn’t originate within our comfort zones.
If we never reevaluate or challenge the way we do things, how would we ever get better? I believe the answer is, we wouldn’t. As the quote often attributed to Albert Einstein states, “insanity is doing the same thing over and over again and expecting different results.”
We must acknowledge our propensity to build repetitive cycles in order to successfully grow our businesses, change and be different. After all, change is the vital element for both success and survival.
With the rapid advancement of technology our world is changing more than ever.
This means our organizations must quickly change, too. It is crucial that we optimize our business practices by looking at our operations and leveraging the resources we use to get things done. In order to grow and prosper, we must recognize our patterns and learn how to change them.
Taking an engineering department for example, your in-house staff may know your business or a particular CAD (Computer Aided Design) package, but are they experts at prototyping, simulation, electronics, and new materials? This is example is where utilizing a fresh perspective could more than benefit your company.
Now look at the systems your company currently depends on.
The methods by which you currently transfer documents, communicate through departments, and transmit information. These are the systems we ultimately forget to challenge. As we become comfortable in our ways, we forget our competitors might be challenging theirs. You might think to yourself.., ‘So what if our department communication may not be the most efficient process’ , but what if speeding up communication would bring your cost down by up to 10 percent! What if your communication systems boosted your competitive advantage, and ultimately accelerated your time to market? These everyday, repetitive processes are what I am challenging you to re-think.
Organizations benefit from change.
A change within an organization results in new ways of looking at customer needs, new ways of delivering customer service, new ways of strengthening customer interactions and new products that might attract new markets. But what many fail to realize is that many of these are driven from internal practices.
If you can imagine the kind of businesses that will all be able to help you improve the products you’re making, then you can see a world where people are able to find a lot more success.
Change is what allows us to explore new opportunities, learn new skills and exercise our creativity.
If nothing else, I challenge you to be fearless in the pursuit of what sets you and your solutions apart. I challenge you to re-think your ways and become the best you can be.