- rinse station
- 2 rinse buckets
- rinse basket
- rinse bottle
- finishing tray
- tweezers
- scraper
- removal tool
- jig
- flush cutters
- disposable nitrile gloves
In our latest episode of the ‘3D Printing Show’, Anthony Bayerl, Director of Marketing, and Lauren Adey, Additive Manufacturing Specialist bring you the latest news in the 3D printing industry. We have some really interesting news this week including 3D printed sushi, 3D printed homes in El Salvador and on Mars, and a new Draft Resin from Formlabs.
Watch our video to learn about the latest additive manufacturing news.
3D Printed Sushi created from.. urine samples?
3D printed ‘8-bit’ sushi | Image Credit: Open Meals
A company called Open Meals in Japan is doing the unthinkable – 3D printing sushi for its customers. But it’s not just any type of sushi… it’s custom 3D printed sushi… created just for you. Open Meals plan to open their restaurant called Sushi Singularity in Tokyo in 2020 and are looking for people to invest in their concept of digitalized food.
They brought their idea to a tech event called South by Southwest (SXSW) in Austin, Texas just this last year. Their booth wowed onlookers as they demonstrated that they are taking people’s individual chemistry from hair, saliva, or urine samples to create sushi full of custom-tailored nutrients that their body needs. The food is printed in a cube-shape, giving them the nickname ‘8-bit sushi’.
Open Meals booth shows off 3D printed sushi at SXSW 2018 in Austin, TX.
The concept is unique – their idea is to create a healthy meal for you based on your body’s nutritional needs. They send you a ‘health test kit’, you return it with a sample of your choice of bodily fluids, and they’ll send back nutrient-rich edible sushi. Open Meals has a plan to send their customized sushi anywhere in the world, as long as you have a suitable food 3D printer.
3D Printed Concrete Houses for Homeless around the World
3D Printed Housing Community in Latin America | Image Credit: www.dwell.com
By the end of 2019, the partnership plans to house over 400 individuals with around 100 homes in a 3D printed housing community in Latin America. While the average ‘tiny home’ price tag is over $25,000, these 600-800 sq. feet concrete houses can be built for around $4000 in less than 24 hours. The homes themselves are built from locally-sourced concrete to be durable and to sustain weather conditions such as hurricanes or tsunamis.
ICON’s portable 3D printer, called the Vulcan II, is built to withstand real-world conditions and restraints in third-world countries such as power shortages, access to water, and limited labor. With only a few workers needed due to the 3D printer’s remote monitoring technology, the homes are built with almost zero waste and are sustainable for several centuries.
New Story and ICON lead the way for future 3D printed homebuilding.
AI SpaceFactory works with NASA to build homes on Mars
3D printing a community on Mars | Image Credit: AI SpaceFactory
AI SpaceFactory is a company comprised of architectural designers and engineers with a desire to build sustainable and eco-friendly habitats on Earth and Mars. Through 3D printing technology, SpaceFactory has developed a 3D printed vertical home or habitat, called MARSHA (MARS HAbitat), that serves as a livable space for humans on Mars.
The structures are built with a double shell system for isolation from extreme temperature swings and harsh conditions on the planet. The first floor consists of a Mars Exploration Rover docking port, a wet lab, and space hatches for entry/exit; the second floor consists of a dry lab and kitchen; the third floor consists of a bathroom, a garden, a sleeping quarters, and an office space; and the fourth floor consists of a ‘sky room’ for exercise and recreational purposes.
MARSHA considers an optimum mental health environment for humans by including windows on every floor with natural sunlight and artificial lighting that mimics Earth-like light.
According to SpaceFactory, MARSHA habitats are made from a mixture of basalt fiber from Mars rock and renewable bioplastic (polylactic acid, or PLA) processed from plants grown on Mars – which is their plan for agricultural sustainability.
Introducing AI SpaceFactory’s MARSHA habitat for living on Mars.
New 3D Printing Draft Resin From Formlabs
Draft Resin, from Formlabs, for multiple design iterations.
The new Draft Resin is three to four times faster than other Standard Resins giving you the ability to cycle through multiple design iterations at a time. Request a free sample of the Draft Resin to see how the material holds up to your standards.
Lauren Adey, our Additive Manufacturing Specialist, can help you choose the right 3D printer or resin for your needs. Make sure to follow her on LinkedIn to see more additive manufacturing news!
If you’re wondering how the Form 3 compares to the Form 2, we’re able to tell you the differences between the two Formlabs 3D printing machines.
Types of 3D Printing
Stereolithography (SLA): a type of vat polymerization where liquid photopolymers resin cures under ultraviolet (UV) light; highly accurate and precise prints; builds 3D layers from the bottom up with support structures.
Digital Light Processing (DLP): the oldest type of 3D printing; a type of vat polymerization where liquid plastic resin cures under LED light; less quality/detail but faster print times than SLA printers.
Fused Deposition Modeling (FDM): most widely-used process; built layer by layer where the thermoplastic filament is heated to melt into a 3D object; slow 3D printing process, but can print large-scale.
Selective Laser Sintering (SLS): uses high-power lasers to fuse particles of powdered substances together; highly accurate and precise prints like SLA printing; builds light-weight prints with no support structures.
Selective Laser Melting (SLM): uses a high-powered laser beam to fuse and melt metallic powders together; used for complex geometries, thin-wall structures; popular uses in aerospace and medical industries.
Electron Beam Melting (EBM): main use is for metal 3D printing; uses powerful electron beam in a vacuum; uses powder bed fusion technique similar to SLM; used for strong, durable 3D prints.
Laminated Object Manufacturing (LOM): heat and pressure fuse plastic, paper, or metal – cut to shape with computer-controlled blade or laser; most affordable and fastest 3D printer used for large-scale rapid prototyping.
The newest type of 3D printing, created by Formlabs, is called:
Low Force Stereolithography (LFS): advanced SLA using a more flexible tank with lower force for even more accurate and precise prints; builds 3D layers from the bottom up with easily removable support structures.
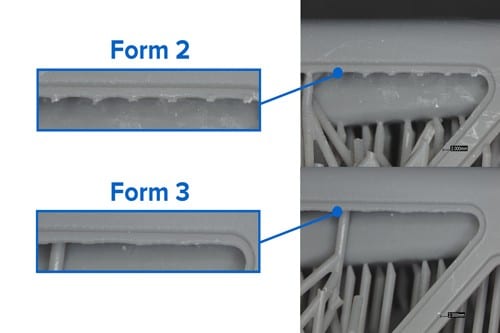
Read more about LFS 3D printing in our blog, Formlabs Releases New 3D Printers using LFS Technology.
Form 2 SLA vs Form 3 LFS
One of the benefits of printing with LFS technology is that the flexible tank significantly reduces stress on parts and prototypes during the peeling process. This results in much clearer parts with an improved surface finish as shown in the following comparison photos of a Form 2 and Form 3 print.
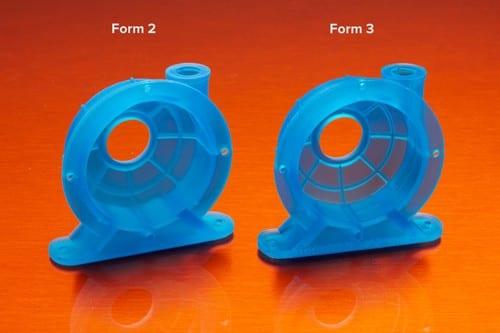
Lower forces with LFS also allows you to capture fine detail and smooth surfaces with minimal layer lines which results in improved quality prints and overall reliability.
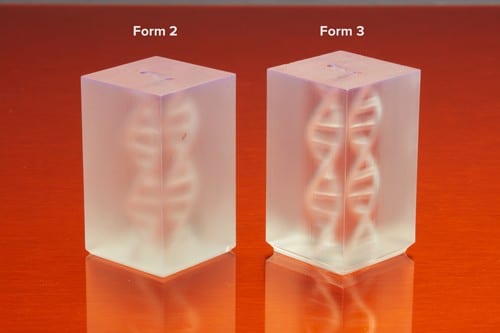
Watch our step-by-step workflow 3D printing with the Form 3 to see Formlabs present on their newest technology!
Look back to my blog on the most frequently asked questions about the Form 2, Form 3 and the Form 3L. Please reach out if you have any questions and don’t forget to follow me on LinkedIn for more news in the additive manufacturing industry!
In our new ‘3D Printing Show’ episode Anthony Bayerl, Director of Marketing, and Lauren Adey, Additive Manufacturing Specialist bring you the latest news in the 3D printing industry.
We talk about new product announcements, tips and tricks, product updates, discounts, and promotions.
Watch our video to learn about the latest additive manufacturing news.
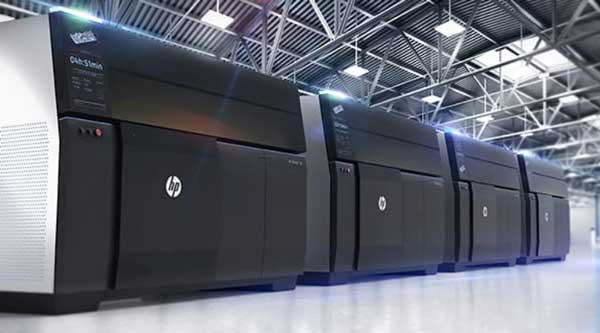
The Future of Metal 3D Printing
Metal 3D printing will pave the way for the future by providing advancements in mass production of 3D printed products such as heat sinks, spare parts, structural components, tooling, medical devices, and industrial automation.
Leading companies like HP are at the forefront of this technology, producing large-scale metal 3D printers that use materials like gold, copper, steel, and titanium to build custom, complex parts.
HP’s article called, Future of Industrial Production: The Metal 3D Printer, points out that we can most likely expect metal 3D printing companies to offer services to print parts and prototypes for other companies in the near future.
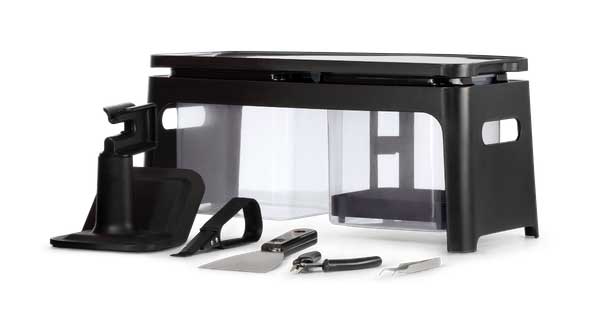
Form 2 Finish Kit
The Finish Kit for the Form 2 helps you stay organized while putting finishing touches on your parts and prototypes.
The Finish Kit includes:
Removing parts after leaving the Form 2 to finish the 3D print overnight
We discuss how Jeff Martin, an Application Engineer from Colder Products (CPC), gives us a tip on how to remove 3D prints from the build platform even when it’s been finished for hours and sitting in the 3D printer.
When you’re printing with material like the rigid resin, it can be difficult to remove if the resin is no longer warm from the finish. Martin suggests using scolding hot water on the surface of the build platform to help scrape off the finished 3D part.
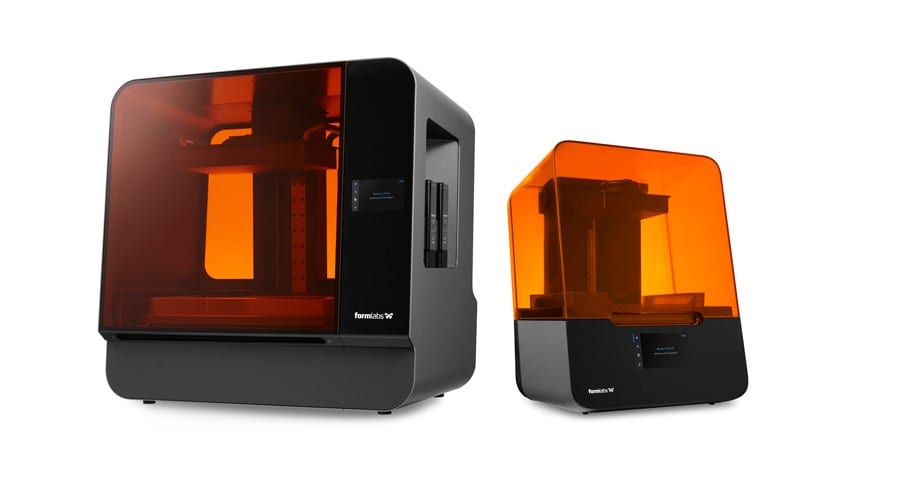
Formlabs Stereolithography 3D Printers: Form 3 and Form 3L
The Form 3 and the Form 3L from Formlabs are here! These 3D printers use a process called low force stereolithography (LFS) for optimum printing details. Read more about the new LFS process in our blog called, Formlabs Releases New 3D Printers using LFS Technology.
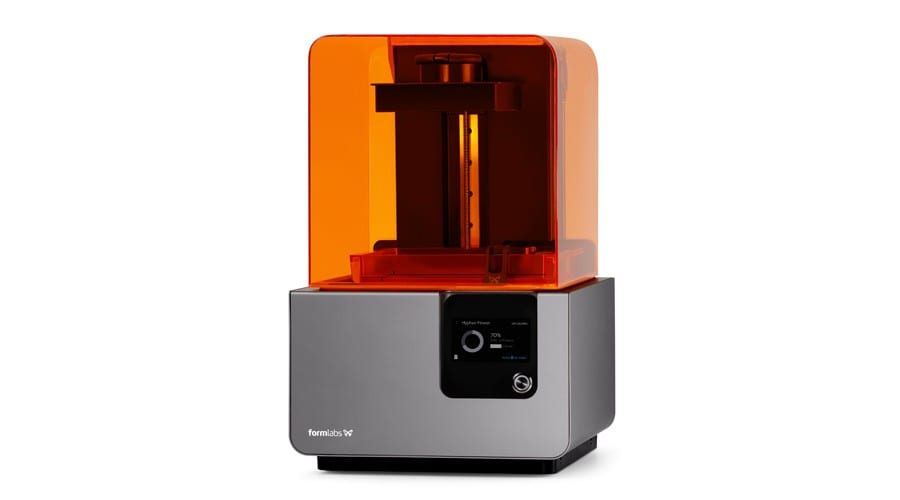
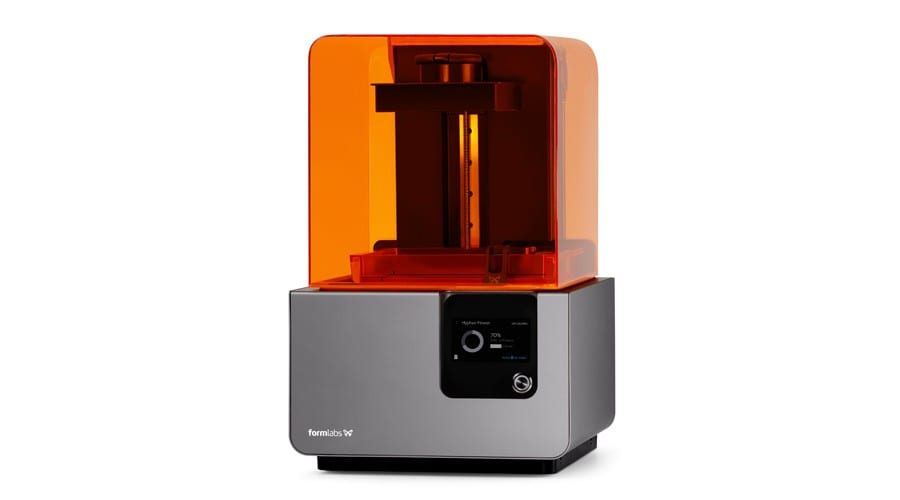
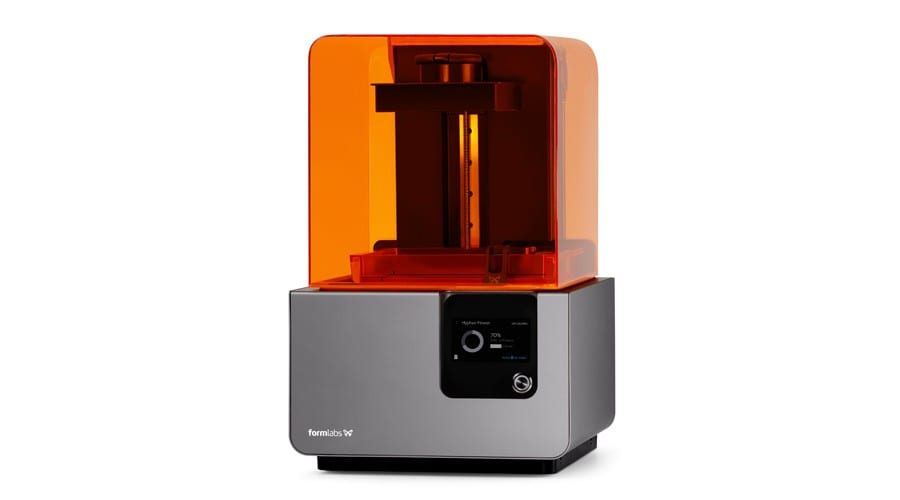
Multiple 3D Printers In-House
In our last post, we mentioned that the Form 2 desktop SLA 3D printer has decreased in price (from its previous price of $3499) to $2850.
If you have always had a print queue, now is the perfect time to buy another 3D printer to use in-house for your parts and prototypes. Now you can excel in rapid prototyping with multiple 3D printers at a low cost.
Read our blog called, 3 Ways 3D Printing In-House Can Transform Your Design Process, to learn how you can benefit from having more than one 3D printer.
Contact Lauren Adey, our Additive Manufacturing Specialist, to take advantage of these special deals! And make sure to follow her on LinkedIn to see more on the latest 3D printing news.
We’d like to share some news with you in our new youtube video we’ve nicknamed the ‘3D Printing Show’. Anthony Bayerl, Director of Marketing, and Lauren Adey, Additive Manufacturing Specialist bring you the latest news in the 3D printing industry.
There are a lot of exciting things happening including new product announcements, tips and tricks, product updates, discounts, and promotions.
Watch our video to learn about the latest additive manufacturing news.
New 3D printer called the ‘Replicator’ makes 3D print in minutes, with almost no wasted material
Stereolithography (SLA) desktop 3D printers, such as the Form 2 from Formlabs, creates 3D prints with photopolymer resin cured with a UV laser and built layer by layer. Structural lattices are created with extra material to ‘fill in’ necessary skeletal-like structures for support to continue to build the part or prototype.
UC Berkeley researchers discovered a new 3D printing technique that transforms liquid on a rotating cylinder to a solid with carefully projected rays of light – without having to waste any extra material in the 3D printing process.
Hossein Heidari, a graduate student at UC Berkeley and co-first author of the work says, “Our technique generates almost no material waste and the uncured material is 100 percent reusable. This is another advantage that comes with support-free 3D printing.”
The researchers named the 3D printer the “replicator” after the Star Trek device that instantly materializes any object. This new technique creates 3D prints in a matter of minutes compared to other techniques that could take hours.
We can’t wait to see where these UC Berkeley researchers take this new zero-waste 3D printing technique!
Creo 6.0 makes software updates to support new lattice structures, build direction, and topology optimization
With the release of Creo 6.0, PTC has updated the additive manufacturing capabilities to design with lattice structures, build direction definition, and slicing. Designing your CAD models with Creo allows you to design, optimize, validate, and run a print-check all in one environment – which means you can send your file straight to the printer when you’re done with your final design. Metal printing capabilities cover around 70% of the metal printers that are sold in the market.
Creo Parametric includes the 3D printing capabilities to directly connect to your printer. These capabilities are included in Creo 5.0 and Creo 6.0.
The Creo Additive Manufacturing Extension includes design abilities such as lattice modeling, advanced beams lattices, custom-defined cells, and defining print build direction. These capabilities are included in the Creo Design Advanced Plus package or you can purchase the extension separately.
The Creo Additive Manufacturing Plus Extension for Materialise includes capabilities to directly connect to metal printers, customize metal support structures, and optimize build direction. These capabilities are included in the Creo Design Premium Plus package or you can purchase the extension separately.
The Creo Topology Optimization Extension includes capabilities to use topology optimization in parts and assemblies and enables geometry reconstruction function. These capabilities are included in the Creo Design Premium Plus package or you can purchase the extension separately.
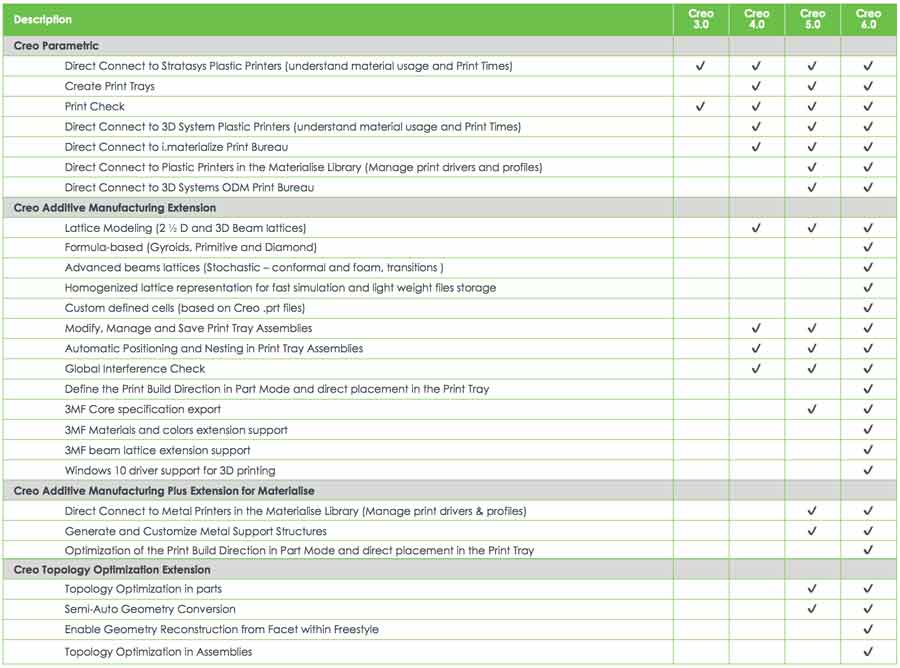
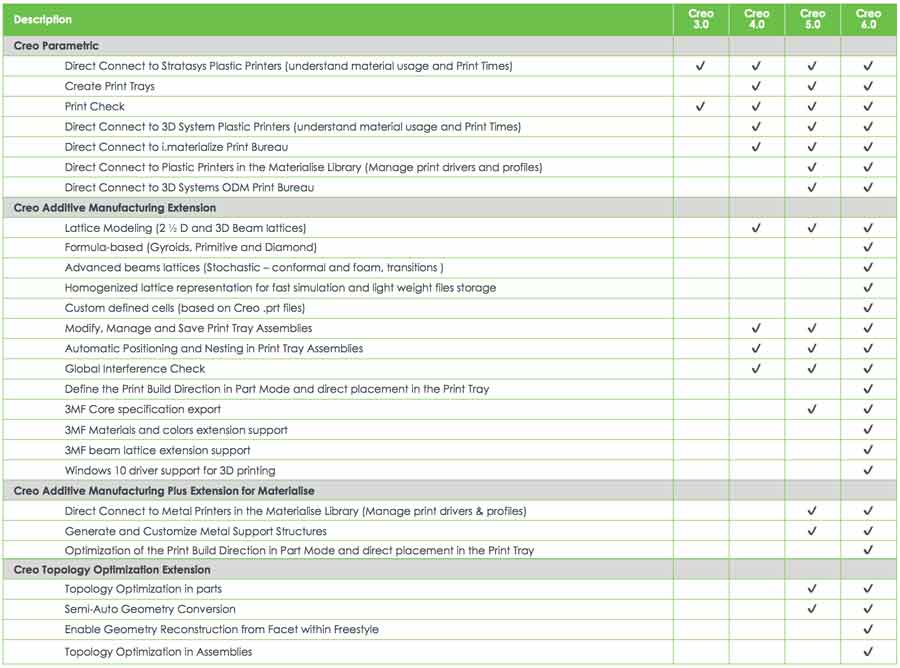
How to wash your parts & prototypes with the Form Wash
We’ve discussed ways that you can better use the products you already own – this time, we’ve got a tip coming from one of our customers – Jeff Martin, an Application Engineer from Colder Products (CPC) on how to clean your parts and prototypes with the Form Wash. Check it out in our blog here.
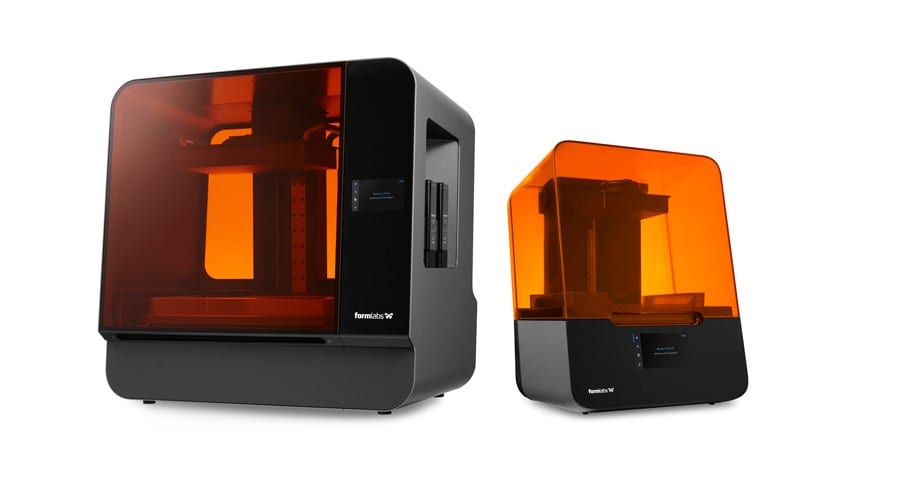
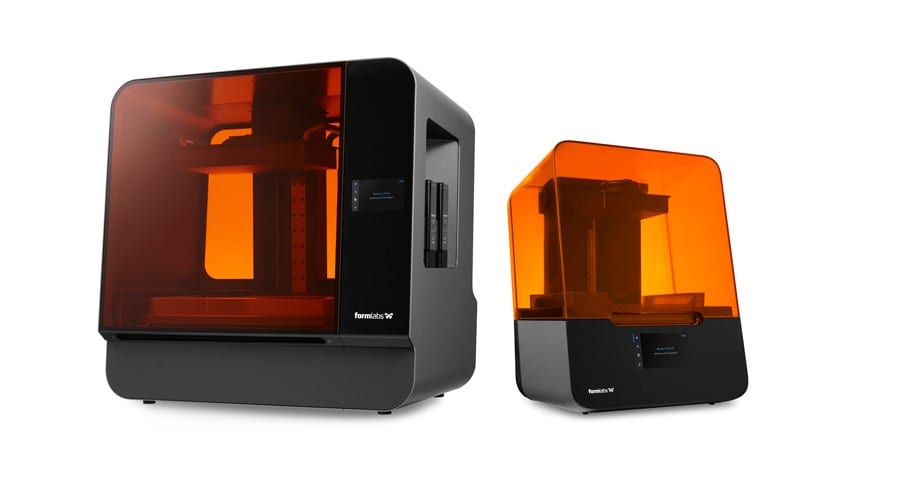
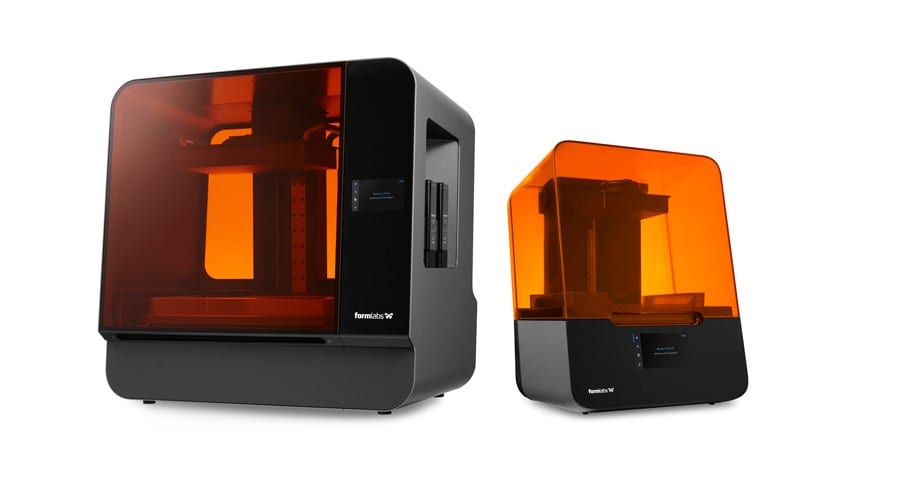
New Formlabs 3D Printers: Form 3 and Form 3L
Formlabs has released the Form 3 and the Form 3L! The Form 2 uses the stereolithography (SLA) process whereas the Form 3 and Form 3L uses a process called low force stereolithography (LFS) – meaning that the printers literally use lower forces to create easier support removal and more precise detail and surface finish. Read our blog Formlabs Releases New 3D Printers using LFS Technology to learn more about SLA and LFS technology.
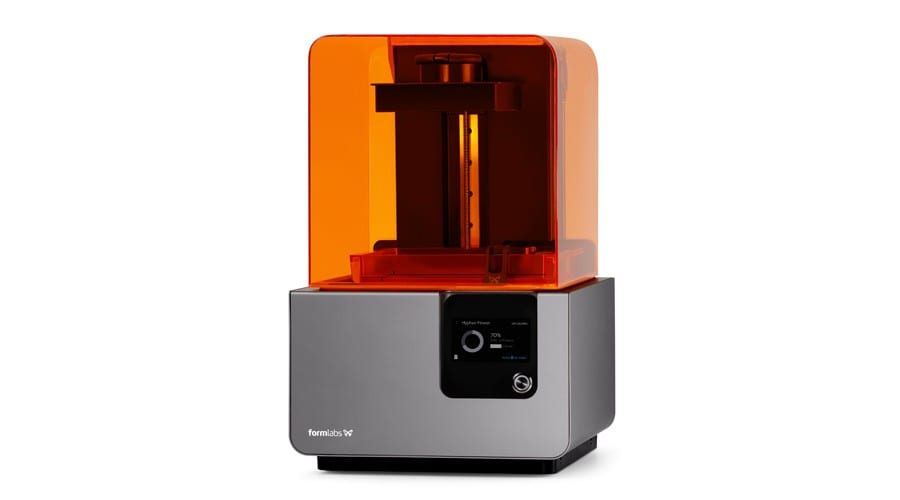
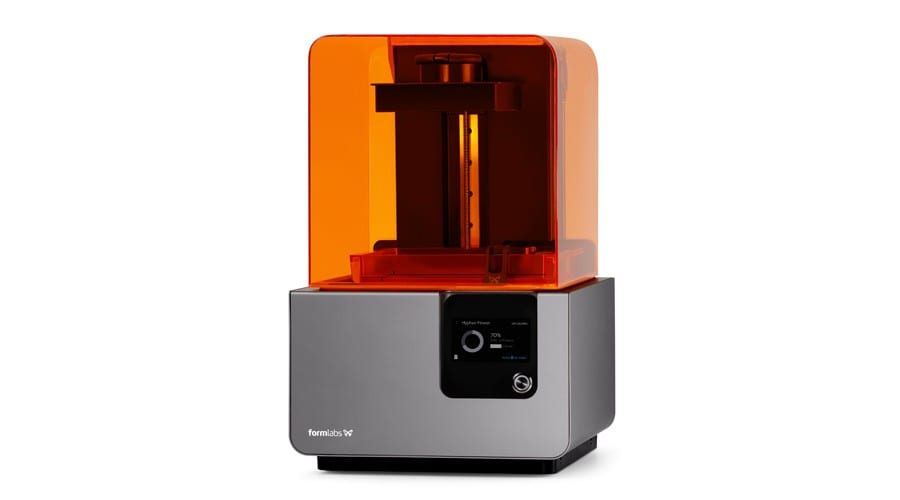
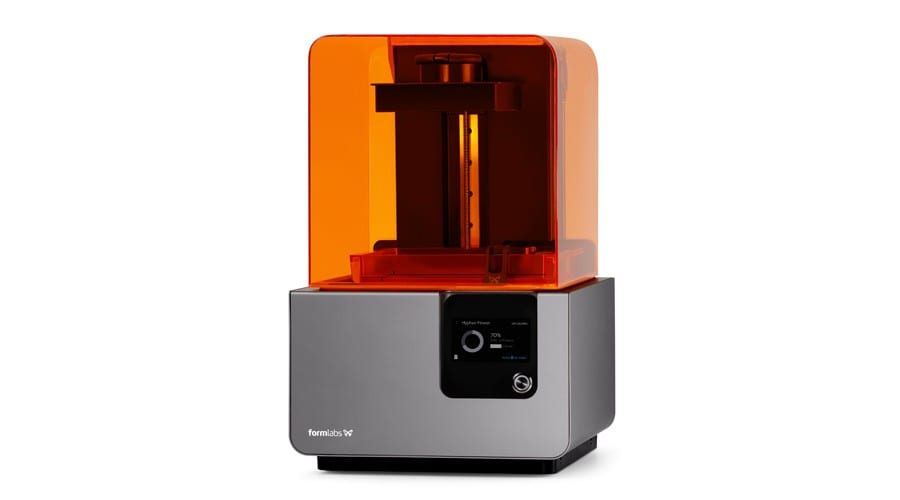
Form 2 Discounts!
The Form 2 desktop SLA 3D printer has dramatically decreased in price (from its previous price of $3499) to $2850. We ARE still selling the Form 2 and will support those that want to purchase an already affordable 3D printer at a more affordable price.
Contact Lauren Adey, our Additive Manufacturing Specialist, to take advantage of these special deals!
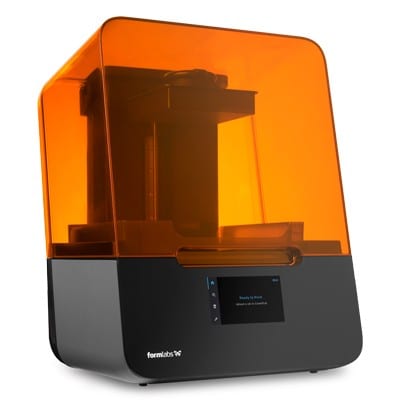
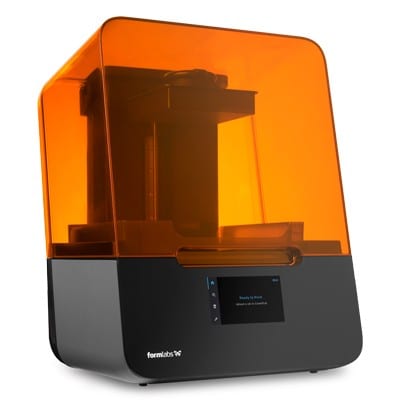
Formlabs 3D Printer: Form 3
What makes the Form 3 the best 3D printer out there?
The Form 3 combines a flexible tank and linear illumination to deliver incredible print quality and printer reliability through a new Low Force Stereolithography (LFS) process.
The flexible tank lowers the forces exerted on the part during printing to provide incredible detail and surface finish, and allows for light-touch support structures that easily tear away. The Light Processing Unit uses a system of lenses and mirrors to direct a precise, uniform high-density laser spot.
How accurate is the Form 3?
The Form 3 prints with 25 micron XY resolution and 25-300 microns (user selectable) in the Z, using an 85-micron laser. Accuracy depends on many factors such as the print performance of an individual resin.
How fast is the Form 3?
The Form 3 delivers the perfect balance of detail and speed. Print times will be comparable to Form 2. A new material, called Draft Resin, was specifically developed for fast printing at 300-micron layers for engineering parts where a fast turnaround is critical.
How does the optics module work?
The custom-designed Light Processing Unit (LPU) inside the printer is built to deliver accurate, repeatable prints, using a compact system of lenses and mirrors. During printing, the LPU moves in the X direction, while the high-frequency galvanometer inside positions the laser beam in the Y direction, then directs it across a fold mirror and parabolic mirror to deliver a beam that is always perpendicular to the build plane. The high-power-density laser is passed through a spatial filter to guarantee a clean laser spot.
What layer thicknesses are available for Form 3?
25 – 300 microns (.001 – .012 in) . See Form 3 tech specs here.
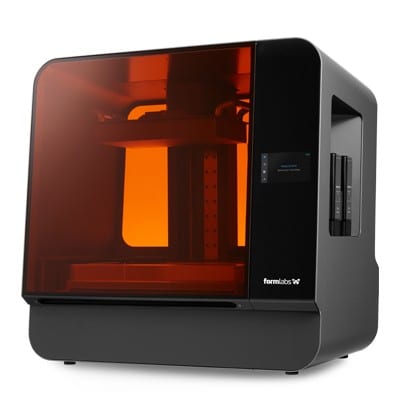
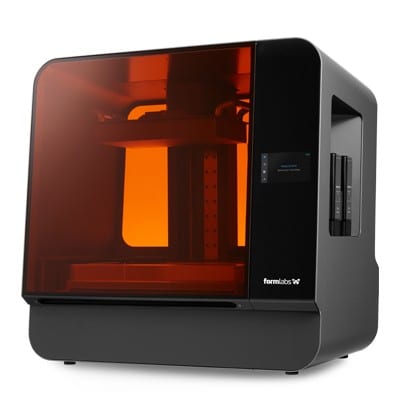
Formlabs 3D Printer: Form 3L
How much bigger is the Form 3L build volume?
Five times bigger than Formlabs’ desktop printers: W x D x H: 33.5 × 20 × 30 cm (13.2 × 7.9 × 11.8 in)
How does the build volume for Form 3 compare to Form 2?
The Form 3 has the same XY (145 x 145 mm) as the Form 2 with a slightly larger Z (185 mm versus 175 mm). See the comparable tech specs here.
What are the biggest differences between Form 2 and Form 3?
The Form 3 is built around a new print process called Low Force Stereolithography. Reducing the forces on parts is key to taking a big leap forward in part quality and printer reliability.
Formlabs has made the core optics more powerful, robust, and easier to monitor and maintain with the enclosed Light Processing Unit. A series of filters, sensors, and mirrors ensure uniform light for greater precision and better performance over time.
They’ve also added many sensors that help with overall usability, from correcting user error with a UI guided onboarding process, to more precisely measuring remaining resin.
Finally, there are some great features designed to save time, increase throughput and enable new ways of working. Like fine touch supports that reduce part finishing time and improve underside surface finish, and the ability to prime a printer to remotely start a print overnight, allowing you to respond to just in time requests.
That said: the Form 2 is an award-winning, tried-and-true machine, and is now available at an even more affordable price point.
How does the Form 3 peel force compare to the Form 2?
The force on a part depends on the part geometry and material. In their internal testing, Formlabs has seen force reductions anywhere from 3 – 10x compared to the Form 2. Reducing the forces on parts while printing allows you to print with fewer and lighter supports. Lower forces also allow us to better capture fine detail and smooth surfaces with minimal layer lines, and result in improved print success and overall reliability.
What parts are cross-compatible between Form 2 and Form 3?
Many components are cross-compatible between the two printers. The build platform, resin cartridges, Form Wash and Form Cure, PreForm, and Dashboard are compatible across both machines. The standard Finish Kits are comparable with the addition of the tank tool for Form 3.
These are the most frequently asked questions for Formlabs’ new 3D printers, the Form 3 and the Form 3L. Please reach out if you have any questions that weren’t answered here.
Don’t forget to follow me on LinkedIn to check out my tips and tricks on how to use Formlabs 3D printers and trends in the additive manufacturing industry!
The next generation of Stereolithography (SLA) 3D printing is here… and we’re here to tell you about it!
Formlabs introduced two new printers, the Form 3 and the Form 3L, using a process called Low Force Stereolithography (LFS) to bring you advanced 3D prints. This new additive manufacturing technology gives you the ability to create better and more affordable parts and enables production-ready applications with higher production volumes.
Let’s get down to the basics.
What is stereolithography (SLA) 3D printing?
The SLA 3D printing process is known for creating a smooth surface finish and detail using a laser to cure solid isotropic parts of liquid photopolymer resin. The Form 2 SLA 3D printer process allows for lower production costs to manufacturers than most 3D printing industrial machines and it leaves a smaller footprint by using less material.
What is Low Force Stereolithography (LFS)?
Low Force Stereolithography (LFS) is an advanced form of SLA printing that uses a flexible tank and linear illumination to turn liquid resin into flawless parts. LFS technology produces all the benefits of SLA technology plus the following features:
- A clean laser spot via a spatial filter ensuring high precision and accuracy
- A parabolic mirror creating a perpendicular laser spot for uniformity across the build platform
- Soft release from a flexible tank enabling easy cleanup by requiring small, minimal supporting
- High performing future materials
- User-replaceable LPU with garage mode to protect optics
- Adaptive print speed for perfect balance of speed and detail
- System scales for large format 3D prints
Low Force Flexible tanks work by the build platform pulling up the part and gently releasing it from the film. When you have a more flexible tank, you get lower force, which allows for better print quality and better printer reliability. Lower forces on the part lead to incredible detail and surface finish, easier support removal, and cutting-edge material possibilities.
The Components of LFS 3D Printing
Condensed optics module: A custom-designed Light Processing Unit (LPU) inside the printer uses a compact system of lenses and mirrors to deliver accurate, repeatable prints.
Flexible Tank: The bottom of the resin tank is a flexible surface that enables a massive reduction in peel forces while printing.
Linear Illumination: The high-powered laser from the LPU coupled with the parabolic mirror provide a crisp completely perpendicular curing source during the LFS 3D printing process.
The Benefits of LFS 3D Printing
- Pinpoint precision for flawless prints
- Balances high detail and high speed
- Faster printing with a high frequency galvanometer
- Many integrated sensors to monitor performance for reliable, nonstop printing
- Fine-touch support touch points
- Better printing for resins with higher viscosity and lower green strength
How linear illumination creates precision and uniformity with parts
Linear Illumination = Precision + Uniformity = Accurate, Repeatable Parts
One galvanometer positions the laser beam in the Y direction. The beam is then directed to a fold mirror and parabolic mirror so the beam is:
1) Always directed perpendicular to the build plane (uniformity/consistency)
2) Always moving in a straight line (precision/accuracy)
What is an LPU and why does it matter?
The LPU is one of the most revolutionary components of Formlabs’ LFS 3D printing technology. The Form 3 contains 1 LPU unit where the Form 3L contains 2.
The LPU holds the laser, the galvanometer, and a system of lenses and mirrors. The parabolic mirror maintains a perpendicular path to the bottom of the resin tank at all times, making for consistently clean, crisp edges and smooth surfaces.
The LPU is a single replaceable part located in the main printer body that folds almost every optical component of the printer into a small metal housing unit.
Rather than containing two galvanometers like the Form 1, Form 1+, and Form 2, the LPU contains just one galvanometer that controls the direction of the laser, as the entire LPU unit moves across the build area.
The main four components of an LPU galvanometer are the fold mirror, the laser, the parabolic mirror, and the galvanometer.
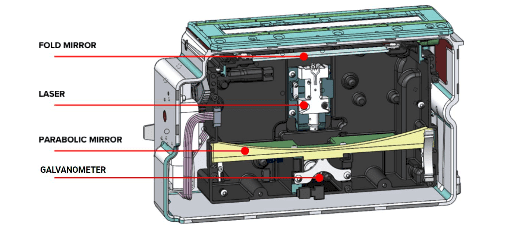
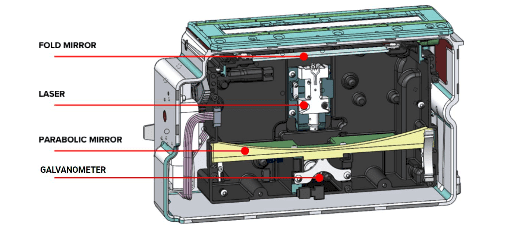
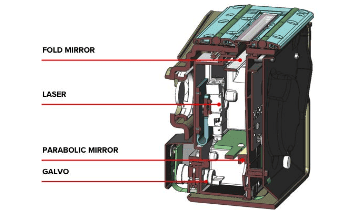
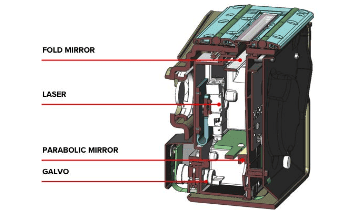
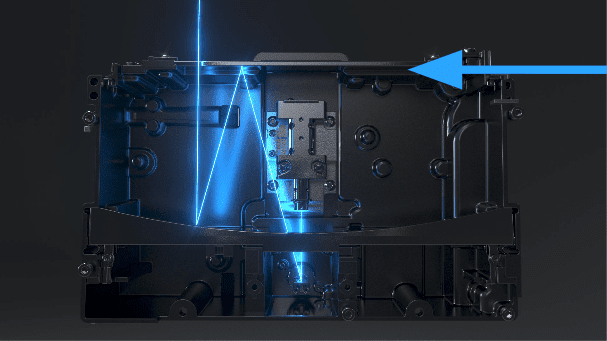
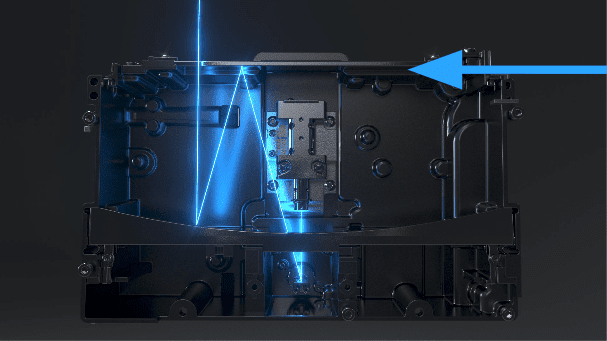


Features of a Light Processing Unit (LPU)
- Highly Precise, Consistent Laser
- Telecentric Laser Beam
- The laser beam in the LPU is always perpendicular and in constant focus at the print plane, thanks to the galvanometer and the parabolic mirror
- This results in the best possible print quality that is uniform, highly accurate, and consistent across the entire print plane
- Telecentric Laser Beam
- Custom high-power module
- Custom high-power-density laser module
- The laser has a spot size of 85 microns (40% smaller than the Form 2!) and a 25% higher power at the print plane due to the improvements in optical path efficiency in the LPU
- This multi-lens system with spatial filtering reduces stray light to sharpen edges even further and ensure consistent, pinpoint precision which creates smoother surfaces and high dimensional accuracy on printed parts
- Custom high-power-density laser module
- Custom high-frequency galvanometer
- The custom galvanometer combined with other features (like adaptive print speed and not needing to use the mixer between layers) allows for fast print times and consistent quality
- Modular and scalable
- Bigger prints (at an affordable price) designed to scale. For the Form 3L, two of the same modules are used as the Form 3
- Self-diagnostics
- Reliability: Constant sensing and automatic calibration
- Field replaceability
- Uptime: No need to swap out your printer to replace the laser or other key optical components
Now that you know how Low Force Stereolithography works, you’re better informed on how you can use Formlabs’ new 3D printers, the Form 3 and the Form 3L.
Reach out if you have any questions, and don’t forget to follow me on LinkedIn to check out my tips and tricks on how to use Formlabs 3D printers and trends in the additive manufacturing industry!